Posts Tagged ‘Manufacturing in China’
OEM vs ODM: Navigating the Manufacturing Maze
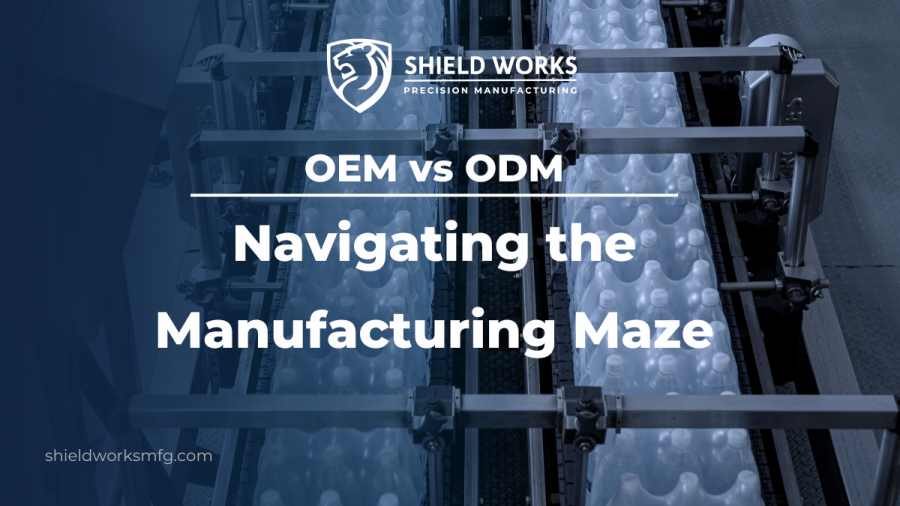
Navigating the manufacturing maze often involves understanding various industry terms and concepts, particularly when it comes to OEM (Original Equipment Manufacturer) and ODM (Original Design Manufacturer). These terms are crucial in the world of product development and manufacturing, especially for businesses looking to outsource these aspects. Understanding the differences between OEM and ODM, as well as their respective advantages and disadvantages, is essential for making informed decisions in the manufacturing process. This comprehensive guide will navigate you through the OEM vs ODM manufacturing maze, helping you make informed decisions that align with your business goals.
Understanding OEM and ODM
What is OEM?
OEM stands for Original Equipment Manufacturer. This term refers to a company that manufactures products or components that are purchased by another company and retailed under the purchasing company’s brand name. OEMs typically work based on the buyer’s design specifications.
Example: A good example is a company that makes computer processors (like Intel or AMD) which are then used in various brands of computers. The computer brands are the clients of the processor manufacturers.
What is ODM?
ODM stands for Original Design Manufacturer. This type of company designs and manufactures a product that is eventually branded and sold by another firm. ODMs provide both design and production services, offering a complete package from product concept to finished goods.
Example: A common example is in the electronics sector, where an ODM might design and manufacture a range of smartphones or gadgets that are then branded and sold by another company.
Key Differences Between OEM and ODM
Understanding the differences between OEM and ODM is crucial in selecting the right manufacturing partner. Here are some key distinctions:
Design Ownership
In an OEM arrangement, the client company retains full ownership of the product design. This means they provide the specifications and blueprints for the product they want to be manufactured. The OEM partner is responsible for producing the product according to these specifications. This level of control allows the client to ensure that the product meets their exact requirements and quality standards.
In contrast, with ODM, the manufacturing company not only produces but also designs the product. The design rights belong to the ODM. Clients choosing an ODM partner typically select from a range of existing product designs and may have some room for minor modifications. However, the core design and technology remain the property of the ODM.
Cost Implications
Opting for OEM manufacturing can be more expensive. This is because creating a product from scratch, with specific design requirements, often involves extensive research and development, as well as the need to create specialized molds or tools. These initial investments can add to the overall cost of the product.
ODM solutions can be more cost-effective, particularly for businesses looking to enter the market with a lower investment. Since ODMs use their existing designs and production processes, the costs associated with design and development are significantly reduced. This can be a more economical option for companies that do not require highly customized products.
Time to Market
The time to market can be longer in OEM arrangements due to the need for custom design and development processes. This includes time for prototyping, testing, and potential redesigns, which can extend the time before the product is ready for launch.
ODM manufacturers typically offer quicker turnaround times. Since they are working with pre-existing designs and have experience in mass-producing these designs, they can modify and produce products more rapidly. This can be a crucial advantage for companies looking to capitalize on market trends or seasonal demands.
Customization Level
OEM is ideal for companies that require high levels of customization. Since the client controls the design, they can specify every aspect of the product, from materials and components to the final appearance and functionality. This is particularly important for companies with unique product requirements or those operating in niche markets.
ODM offers limited customization. The modifications are generally restricted to aspects like branding, color schemes, and minor feature changes. This is suitable for businesses that are satisfied with existing product designs and do not need extensive alterations.
Intellectual Property
In an OEM partnership, intellectual property concerns are typically more straightforward. The client company, owning the design, retains the IP rights. This clear delineation can provide a sense of security and is crucial for companies whose value is tied to their proprietary designs and technology.
IP rights in an ODM arrangement can be more complex. Since the design belongs to the manufacturer, the client needs to negotiate the terms of use, including where and how the product can be sold, and any exclusivity arrangements. Understanding and negotiating these terms is critical to avoid potential legal issues and to ensure that the client’s interests are protected.
Choosing Between OEM and ODM
When faced with the decision of selecting between OEM and ODM for product development and manufacturing, various critical factors come into play. Here’s an expanded view of these considerations:
Nature of the Product
This approach is ideal for highly specialized or innovative products. If your product requires specific design, unique features, or proprietary technology, OEM allows for greater customization and exclusivity. In OEM, the manufacturer builds the product based on your exact specifications, ensuring that your vision for a unique product is realized.
On the other hand, ODM is suitable for more generic or standard products. If your product does not demand unique specifications and can be adapted from existing designs, ODM is a practical choice. ODM manufacturers offer their designs and products, which you can rebrand and sell. This is particularly beneficial if the product is common and does not require significant differentiation in the market.
Budget Constraints
Generally, OEM requires a higher investment due to the need for custom design, development, and tooling. If your budget allows for these expenses and the expected ROI justifies the initial costs, OEM can be a worthwhile investment.
For businesses with tighter budget constraints, ODM is often more cost-effective. Since the product is already designed and tested by the manufacturer, the costs associated with design and development are significantly reduced. This makes ODM a popular choice for startups and small businesses looking to launch products without heavy upfront investments.
Market Strategy
If your market strategy revolves around brand uniqueness and creating a distinct product identity, OEM is the way to go. It allows for greater customization, enabling you to develop products that can be patented and stand out in the market. This is particularly important in industries where brand differentiation is a key competitive advantage.
If the strategy is to enter a market quickly with a product that does not necessarily need to be unique, ODM is more suitable. It allows companies to leverage existing market trends with products that are already popular, reducing the risk associated with market acceptance.
Time Constraints
The OEM process is typically more time-consuming, as it involves developing a product from scratch, including design, prototyping, and testing phases. If time to market is not a critical factor, and you can afford a longer development cycle, OEM allows for a tailored product development process.
For businesses looking to launch products quickly, ODM offers a significant advantage. Since the products are already developed and often just need rebranding, the time from concept to market is substantially shorter. This is particularly advantageous in fast-moving industries where being first to market can be crucial.
Quality Control
If maintaining strict quality control is vital, OEM provides more oversight and control over the manufacturing process. You can specify materials, components, and production methods, and have greater involvement in quality assurance processes.
While ODM still maintains a level of quality, the control over production is less compared to OEM. The designs and processes are predetermined by the manufacturer, which might not always align with your specific quality standards. However, for products where extreme customization is not required, ODM can still offer a reliable level of quality.
Best Practices in Partnering with OEMs and ODMs
The choice between OEM and ODM manufacturing depends on various factors. Each model offers distinct advantages and challenges, and the right choice varies based on individual business needs and goals.
Remember, the key to successful manufacturing lies not just in choosing between OEM and ODM, but also in selecting the right manufacturing partner, negotiating favorable terms, and maintaining quality and compliance.
For more guidance and expert insights into navigating the complexities of OEM and ODM when outsourcing manufacturing to China, feel free to contact us. Our team of seasoned professionals is equipped to help you make strategic decisions that align with your business objectives and market dynamics.
Navigating Intellectual Property Protection When Manufacturing in China
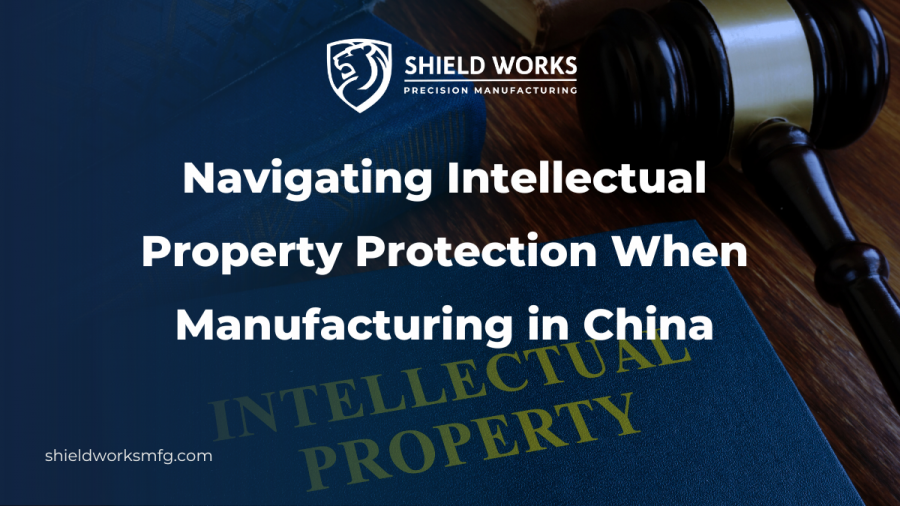
In the global business landscape, China has emerged as a powerhouse in manufacturing. For many companies, the allure of cost-effective production, vast supply chains, and rapid scalability is irresistible. However, this opportunity comes with its own set of challenges, particularly in the realm of intellectual property (IP) protection. In this comprehensive guide, we’ll navigate the complexities of safeguarding your IP when manufacturing in China, ensuring your innovations remain your own.
Understanding Intellectual Property: The Basics
Before you outsource your production to China, it is important to understand what happens to your intellectual property rights (IPR) once you outsource to a Chinese manufacturer.
What is Intellectual Property?
At its core, intellectual property refers to creations of the mind – inventions, literary and artistic works, symbols, names, images, and designs used in commerce. It’s a broad category that encompasses various types of assets, each with its own rules and methods of protection.
Types of Intellectual Property
- Patents: Protect inventions and improvements to existing inventions.
- Trademarks: Safeguard logos, names, and slogans used to identify goods or services.
- Copyrights: Cover artistic and literary works like books, music, and software.
- Trade Secrets: Involve formulas, practices, or processes that are not generally known and offer a competitive advantage.
Understanding the Importance of IP in Manufacturing
Understanding the importance of Intellectual Property (IP) in manufacturing is crucial for businesses to maintain a competitive edge, foster innovation, and ensure economic growth. Intellectual Property refers to creations of the mind, such as inventions; literary and artistic works; designs; and symbols, names, and images used in commerce. In the context of manufacturing, IP plays a pivotal role in several ways:
The Foundation of Competitive Advantage
In manufacturing, IP is more than just a legal concept; it’s the foundation of your competitive advantage. It encompasses everything from product designs and manufacturing processes to brand names and trade secrets. Effective IP management ensures that these assets are not only protected from infringement but also strategically used to establish market dominance.
Risk Mitigation
Before manufacturing begins, assessing potential IP risks is crucial. This involves conducting thorough patent searches to avoid infringement and understanding the IP landscape of your market. By identifying these risks early, you can devise strategies to mitigate them, ensuring a smoother path to market entry.
The Evolution of IP Laws in China
China’s journey towards robust IP laws has been a work in progress. Over the past few decades, the country has revamped its legal framework to better align with international standards, especially after joining the World Trade Organization (WTO) in 2001. However, understanding the nuances of these laws is crucial for foreign businesses.
Key IP Regulations
China’s IP protection revolves around three main areas: patents, trademarks, and copyrights. The Chinese patent system includes invention patents, utility model patents, and design patents. Trademarks in China operate on a first-to-file basis, which is different from the first-to-use system in some other countries. Copyrights, meanwhile, protect literary, artistic, and scientific works.
Strategic IP Management Before Manufacturing
Strategic intellectual property (IP) management is crucial before embarking on the manufacturing process, especially for businesses looking to safeguard their innovations. Here’s a guide to strategic IP management before manufacturing:
Aligning IP with Business Goals
Your IP strategy should be a reflection of your broader business objectives. This alignment ensures that every patent, trademark, or design registration supports your market position and contributes to your company’s growth and profitability.
Prioritizing IP Assets
Not all IP assets hold the same value. It’s essential to identify which inventions, designs, or trademarks are critical to your business and allocate resources accordingly. This prioritization helps in focusing efforts on IP that offers the highest return on investment.
Conducting Thorough Due Diligence
Before partnering with a Chinese manufacturer, it’s essential to conduct comprehensive due diligence. This includes researching potential partners’ backgrounds, understanding regional differences in IP enforcement, and being aware of prevalent IP challenges in your industry.
Securing Your IP Portfolio
Register your patents, trademarks, and copyrights with the China National Intellectual Property Administration (CNIPA). Given the first-to-file system for trademarks, prioritize this to prevent “trademark squatting.”
Leveraging Contracts and NDAs
When dealing with Chinese manufacturers, detailed contracts and Non-Disclosure Agreements (NDAs) are your first line of defense. Ensure these documents are comprehensive and enforceable under Chinese law.
Collaborating with Chinese Manufacturers
Choosing the Right Partner
Selecting a trustworthy manufacturing partner is critical. Look for companies with a good reputation and a track record of respecting IP rights. Sometimes, splitting your manufacturing between multiple factories can reduce the risk of IP theft.
Monitoring and Compliance
Regular audits and inspections can help ensure your IP is being respected on the ground. Consider working with local experts or agencies that specialize in IP law and on-site factory audits.
Staying Ahead of the Curve
IP protection in China is not a set-and-forget strategy. Stay informed about changes in Chinese IP laws and adapt your strategies accordingly. Regularly update your contracts, NDAs, and registrations to cover new products or changes in your business.
Embracing Innovation and Secrecy
Sometimes, the best defense is keeping your most crucial trade secrets just that – secret. Limit the amount of sensitive information shared and consider keeping key components of your product or process outside of China.
Conclusion
Navigating IP protection in China requires a proactive and informed approach. By understanding the legal landscape, preparing thoroughly, choosing the right partners, and staying vigilant, businesses can mitigate the risks associated with manufacturing in China. Remember, the protection of your intellectual property in China is not a one-time effort but an ongoing process. It requires continuous attention and adaptation to new challenges and changes in the market and legal environment.
For more insights or personalized advice on protecting your intellectual property in China, do not hesitate to contact us today. Our team of experts, with their deep understanding of both the legal landscape and the market dynamics in China, is here to guide you through every step of your journey. We are committed to ensuring that your innovations and intellectual assets are effectively safeguarded, allowing you to focus on growing your business with confidence in the Chinese market and beyond.
How to Increase Manufacturing Optimization

Businesses are losing trillions of dollars from unhappy and dissatisfied customers every year. Becoming a top manufacturer is one way to minimize the risk of angry customers.
The best manufacturers are reliable, flexible, and ethical. They communicate well and do everything in their power to streamline the manufacturing process.
Manufacturing optimization should not compromise quality. The right strategies and tips can help you become a leader in the manufacturing industry. Keep reading to learn what they are.
Techniques for Manufacturing Optimization
Some specific tools and strategies can help manufacturers improve the production process. Increasing optimization should involve holistic improvements.
Depending on your business, some techniques may work better for you than others.
Just-in-Time (JIT) Manufacturing
Just-in-time (JIT) manufacturing involves manufacturing products as they are needed. This is ideal for smaller businesses that want to reduce waste. JIT can also minimize inventory and improve overall efficiency.
JIT works best for optimization when combined with other manufacturing techniques.
Total Quality Management (TQM) Manufacturing
Total quality management (TQM) manufacturing places an emphasis on operational quality. Through continuous improvement, TQM can help a manufacturer:
- Improve product quality
- Increase customer satisfaction
- Reduce defects
TQM focuses not only on the customer but also on how employees are involved in the manufacturing process.
Statistical Process Control (SPC)
Statistical process control (SPC) uses a lot of numbers to optimize manufacturing. Manufacturers will use statistical methods to correct variations that are found.
This strategy works to improve manufacturing optimization by reducing waste and improving the consistency of products.
Lean Manufacturing
Lean manufacturing works well with JIT manufacturing. The focus stays on maximizing value by minimizing waste.
Eliminating non-value-added activities is one of the main components of lean manufacturing. The great thing about lean manufacturing is that it works for many industries.
How to Increase Manufacturing Optimization
It’s important to optimize manufacturing to make it as efficient as possible. By reducing delays and eliminating waste, your business can push out products faster without compromising quality.
Optimizing manufacturing leads to:
- Fewer production delays
- Improved product quality
- Better operational visibility
- Resource allocation
By identifying inefficiencies in your manufacturing process, you become more productive. You can begin optimizing your process by utilizing these tips:
Track and Analyze Data
Manufacturers should have access to production data where they can track and analyze their performance. By using the right software and equipment, a business can track production in real time.
If you manually track data, consider a more modern approach. Paper tracking is error-prone and increases the risk of downtime.
When you see what’s happening throughout the manufacturing process, you identify more optimization opportunities.
After taking a long look at your data, you may find that there are inefficient processes in your production process. Change any operating steps that negatively impact production flow.
Analyze the data to recognize areas of inefficiency. With your findings, you can optimize the impacted areas to increase productivity from there on out.
Conduct a Bottleneck Analysis
A bottleneck is not ideal in the manufacturing process. Every manager knows what they are, but not all know how to deal with them. If you have a bottleneck that is slowing down your overall production, find it and deal with it.
Conducting a bottleneck analysis allows you to identify constraints, such as scheduling or production disruption.
Tracking and analyzing data will help you understand each stage of your manufacturing process. If a step in the process gets a workload that exceeds capacity, a bottleneck is likely.
Find the root cause of the problem and then decide on an ideal solution. If scheduling is the issue, for example, hire more staff to overcome labor shortages. You can also use past data to prepare for rush orders.
A machine downtime analysis is useful for bottlenecks that need to be addressed right away. Tracking key performance indicators (KPIs) like Mean Time Between Failure and Mean Time to Repair can aid in optimization.
Manufacturing Automation
Automation tools are taking over many industries, and manufacturing is no different. Automating certain processes can lead to more efficient production.
Manufacturing businesses gain efficiency when they automate labor-intensive, manual tasks. Still, there is a need for human involvement. Workers and automation tools should work together seamlessly to achieve goals.
Some of the common tasks that manufacturers can automate are:
- Data entry
- Inventory management
- Production monitoring
- Supply chain management
- Quality control
Optimizing the manufacturing process must include automation and humans that can add cognitive input into the process.
Utilize Technology
By using technology, manufacturers have many opportunities to optimize manufacturing. You can find and utilize tools and technologies that benefit your needs.
High-tech computer programming is a great way to manufacture different products. Plus, it can be automated.
Another important technology to consider is an ERP system that offers:
- Production planning
- Inventory management
- Manufacturing coordination
- Process scheduling
ERP systems allow manufacturers to improve their processes and streamline productivity. These systems are scalable and can work with manufacturers through business growth.
The popularity of artificial intelligence (AI) can help manufacturers too. This technology leads to real-time data analysis through machine learning.
Review Your Plan
Manufacturing optimization comes in many different forms. What works now might not work in the future.
To ensure you are getting the most out of your production process, measure your progress over time. Review your plan to see where you can implement new and improved manufacturing tools and tips.
Keep track of the changes within your business and the trends surrounding the industry. With this information, you can keep improving your production process.
Improve Your Production Process Now
There is a lot that goes into a manufacturing business. If you want to be more efficient and optimize the process, consider outsourcing.
Shield Works Precision Manufacturing provides customized manufacturing solutions and more. Manufacturing optimization involves delivering products on time and allowing open communication. We are professionals at both.
With 16 years of China-based manufacturing, our highly skilled team can improve your production process. Our added reassurance and security is unmatched in the industry.
Get in touch with our team to get started.
Overcoming Challenges in Quality Control for Manufacturing in China

In the intricate world of global manufacturing, maintaining stringent quality control standards is paramount, especially in a powerhouse like China. Quality control in manufacturing in China encompasses a myriad of procedures aimed at ensuring products not only meet but exceed predefined criteria and customer expectations. However, navigating the complexities of quality assurance within the Chinese manufacturing landscape presents unique challenges. This blog post delves into the multifaceted approach required to surmount these obstacles, ensuring the delivery of high-quality products consistently.
Understanding the Importance of Quality Control in Manufacturing
At the heart of any successful manufacturing operation lies a robust quality control (QC) system. This critical function serves as the guardian of product excellence, ensuring that every item produced meets rigorous standards of quality and reliability. In the context of manufacturing, QC is a comprehensive process that involves the detailed inspection and testing of materials, components and finished goods.
The objective is to identify and rectify any deviations or defects before products reach the consumer, thereby safeguarding the integrity of the brand and fostering customer trust.
Furthermore, a well-executed quality control strategy is instrumental in reducing waste and cutting unnecessary costs, as it helps to catch issues early in the production cycle. This not only protects the manufacturer from the financial and reputational damage associated with poor-quality products but also reinforces a competitive edge in the market by consistently delivering superior value to customers.
The Unique Challenges of Quality Control in China
Tackling quality control within China’s vast manufacturing environment brings forth distinct obstacles. The expansive and diverse manufacturing base means companies often grapple with maintaining uniform quality standards across multiple production facilities, which can vary significantly in their practices and capabilities. This heterogeneity poses a significant challenge in ensuring consistent product quality.
Furthermore, the drive to minimize costs and accelerate production timelines can inadvertently pressure quality control processes, leading to potential compromises in product integrity.
The cultural and linguistic nuances further complicate these dynamics, as effective quality management requires not just technical adherence but also deep cultural understanding and clear communication channels.
Additionally, navigating the regulatory landscape, which can differ markedly from Western standards, adds another layer of complexity to maintaining stringent quality controls. These challenges necessitate a tailored approach that respects China’s unique manufacturing ecosystem while upholding the highest quality standards.
Establishing Effective Communication and Understanding Cultural Differences
Bridging the communication gap is fundamental, which means employing bilingual staff or skilled translators is just the first step. To truly foster a collaborative environment conducive to high-quality outcomes, companies must go beyond language. They should invest in cultural training for their teams to grasp the subtleties of Chinese business practices and social etiquette. Such initiatives pave the way for more effective interactions and negotiations, setting the stage for clearer conveyance of quality expectations and procedures.
Engaging with local manufacturers and suppliers in a manner that respects their cultural context enhances mutual respect. This, in turn, facilitates a smoother implementation of quality control measures and encourages a more dedicated adherence to these standards. Emphasizing respect for cultural differences and prioritizing clear, respectful communication strategies are essential components in the toolkit for overcoming quality control challenges in China’s dynamic manufacturing landscape.
Implementing International Quality Standards
Adopting international quality standards, such as ISO 9001, is a pivotal step in addressing the myriad of challenges presented by quality control in manufacturing within China.
These universally recognized frameworks facilitate a common understanding and establish clear guidelines for quality management practices, bridging the gap between different operational cultures. By integrating these standards into their quality control processes, manufacturers can ensure a consistent approach to quality management across diverse production sites, irrespective of geographical and cultural disparities.
Certification to such standards not only enhances the credibility of the manufacturer on a global scale but also reassures customers of the company’s dedication to maintaining high-quality outputs. It allows for the setting of precise quality benchmarks, streamlining the evaluation of manufacturing processes and ensuring alignment with international expectations.
Leveraging Technology for Enhanced Quality Control
The integration of cutting-edge technology into quality control systems presents a transformative approach to addressing quality assurance challenges in China’s manufacturing sector.
Automation tools and AI have the potential to revolutionize traditional QC methods by enabling real-time monitoring and predictive analytics. These technologies facilitate early detection of potential quality issues, significantly reducing the risk of defects.
For instance, automated inspection systems equipped with high-resolution cameras and sensors can perform detailed checks at a speed and accuracy unattainable by human inspectors. Similarly, AI-driven analytics can sift through vast amounts of production data to predict quality deviations, allowing preemptive corrective actions.
Building a Quality-Centric Manufacturing Ecosystem
To effectively build a quality-centric manufacturing ecosystem, it is imperative to weave the ethos of quality into the fabric of the organization. This initiative should start from the leadership and seamlessly permeate through every stratum of the company, reaching down to the operational level. It is critical to cultivate an environment where every employee, from executives to line workers, views themselves as a vital component of the quality assurance process.
This collective responsibility mindset encourages the identification, reporting, and rectification of quality issues at the earliest stages, fostering a proactive approach to quality management. Implementing training programs focused on quality awareness and best practices further equips the workforce with the necessary tools and knowledge to contribute effectively to the organization’s quality objectives.
Strategies for Continuous Improvement in QC
In the relentless pursuit of excellence within the realm of quality control, employing methodologies such as Six Sigma and Total Quality Management (TQM) is indispensable.
These strategies underscore the importance of systematic, data-driven approaches to minimize defects and enhance efficiency. By fostering a culture that embraces continuous learning and improvement, manufacturers can stay abreast of the latest technological advancements and QC techniques. This involves not only regular training sessions but also benchmarking operations against recognized industry standards to identify areas for enhancement. The adoption of innovative practices and tools is vital for refining quality control mechanisms.
Additionally, extending quality expectations to the supply chain through supplier development programs ensures a comprehensive embrace of quality standards. This holistic approach to improvement keeps quality control processes dynamic, allowing them to evolve in alignment with both technological progress and the shifting landscapes of consumer demand and regulatory compliance.
Elevate Your Manufacturing Excellence
As you embark on this journey to ensure top-tier quality in your manufacturing processes, remember that continuous improvement is the key. Stay agile, adapt to changes, and consistently refine your quality control measures to meet the evolving demands of the market.
If you’re ready to take the next step in enhancing your quality control processes or if you have specific questions tailored to your business needs, don’t hesitate to reach out to us. Our team at Shield Works comprises experienced professionals who bring a wealth of knowledge and a deep understanding of the nuances in various industries. We are dedicated to helping businesses like yours overcome obstacles, streamline operations, and elevate the standard of your products and services. Our approach is tailored to meet the specific challenges and objectives of your business, ensuring that our solutions are not just effective but also aligned with your unique requirements.
Whether it’s a general inquiry or a specific challenge you’re facing, our team is ready to provide the guidance and support you need to achieve excellence in your business operations. Let’s work together to create a future where quality and efficiency drive your business forward.
How Precision Manufacturing in China is Redefining Industry Standards

Precision manufacturing in China is revolutionizing the global manufacturing industry. By utilizing advanced technology and innovative methods, Chinese manufacturers are achieving high precision in their manufacturing processes, pushing the boundaries of what is possible with manufacturing. This is having a profound impact on industry standards, with precision manufacturing in China leading the way in terms of quality, speed, and efficiency. In this blog post, we’ll explore how precision manufacturing in China is redefining industry standards.
What is Precision Manufacturing?
Precision manufacturing is a cutting-edge approach to production that aims to create intricate and high-quality components or products with utmost accuracy and precision. It involves using advanced technology and innovative techniques to achieve tight tolerances, ensuring that each piece is manufactured with exactitude. This method requires meticulous planning, precision tools, and skilled technicians who have a keen eye for detail.
Unlike traditional manufacturing methods, precision manufacturing focuses on achieving perfection in every step of the process, from design to production. This includes using computer-aided design (CAD) software to create detailed and precise blueprints, as well as employing state-of-the-art machinery like CNC machines and 3D printers to fabricate the components.
The Importance of Precision Manufacturing
Precision manufacturing is of utmost importance in today’s highly competitive and fast-paced industry. It allows for the creation of intricate and complex components that power various sectors, from aerospace to medical devices. The precision achieved through this manufacturing approach ensures that every product is produced with the utmost accuracy and meets the highest quality standards.
One of the key benefits of precision manufacturing is its ability to produce components that traditional manufacturing methods simply cannot achieve. The advanced technology and innovative techniques employed in precision manufacturing enable manufacturers to create highly precise and intricate designs that were previously thought to be impossible. This opens up a world of possibilities for industries that rely on precise components, pushing the boundaries of what is achievable.
Moreover, precision manufacturing in China is revolutionizing the global manufacturing industry by leading the way in terms of quality, speed, and efficiency. Chinese manufacturers have invested heavily in state-of-the-art machinery and have cultivated a skilled workforce that excels in precision manufacturing. This has positioned China as a global leader in precision manufacturing, setting new industry standards for others to follow.
Applications of Precision Manufacturing
Precision manufacturing has a wide range of applications across various industries, where high accuracy and quality are crucial. One of the key sectors that greatly benefits from precision manufacturing is aerospace. The aerospace industry requires components that are not only precise but also lightweight and durable. Precision manufacturing techniques enable the production of intricate parts like turbine blades, engine components, and aerospace structural elements with impeccable precision, ensuring safety and efficiency in air travel.
Another industry that heavily relies on precision manufacturing is the medical field. From surgical instruments to implantable devices, precision manufacturing plays a critical role in producing components that are reliable and safe for medical use. The ability to create complex designs and tight tolerances ensures that medical devices function as intended and can be used with confidence by healthcare professionals.
Precision manufacturing also finds extensive applications in automotive manufacturing. From engine components to suspension parts, precision manufacturing ensures that vehicles operate at optimal performance levels. High precision ensures that parts fit together perfectly, reducing friction and improving overall vehicle efficiency.
Additionally, the electronics and telecommunications industries benefit from precision manufacturing. The production of miniaturized electronic components, circuit boards, and connectors requires the utmost precision to ensure functionality and compatibility with other electronic systems.
Technologies Used in Precision Manufacturing
Precision manufacturing relies on a range of advanced technologies to achieve high levels of accuracy and precision. One of the key technologies used in precision manufacturing is computer-aided design (CAD) software. CAD allows manufacturers to create detailed and precise blueprints, which serve as the foundation for the manufacturing process. It enables engineers to design intricate components with exact measurements and specifications, ensuring that each piece is manufactured with precision.
In addition to CAD, precision manufacturing also utilizes state-of-the-art machinery such as CNC machines and 3D printers. CNC machines are capable of producing complex shapes and intricate designs with incredible precision. They can perform multiple operations, such as cutting, drilling, and milling, with high accuracy, resulting in finished components that meet the tightest tolerances.
3D printers, on the other hand, enable manufacturers to create three-dimensional objects from digital models. They use additive manufacturing techniques to build layers of material until the final product is complete. 3D printing is particularly beneficial for producing prototypes and small batches of custom components quickly and cost-effectively.
Stay Ahead of the Game with Shield Works
In the dynamic landscape of global manufacturing, choosing the right precision manufacturing partner can make all the difference. When considering offshore production, companies often seek the assurance of Western standards and management. This assurance is precisely what Shield Works provides.
- Western Management Excellence: Our Western management background sets us apart. We understand the stringent quality expectations and positive interactions that overseas companies seek. This understanding guides us in delivering exceptional outcomes.
- IP Rights Security: At Shield Works, security is paramount. We specialize in providing comprehensive security solutions to safeguard your IP rights. Whether it’s contract manufacturing or product assembly, we ensure the utmost protection throughout the process.
- Rigorous Process, Consistent Results: Our meticulous process ensures that every step, from order placement to final delivery, adheres to rigorous quality standards. Consistency is not just a goal but a practice we uphold with every project.
At Shield Works, we don’t just meet industry standards; we set them. Experience security, excellence, and peace of mind like never before. Your success is our commitment. Contact us today to unlock a world of possibilities.
Leveling Up Your Product Manufacturing in China: Working with a Western-Owned Partner

Are you considering product manufacturing in China for your business but worried about the potential pitfalls of working with a manufacturer? If so, it may be worth exploring the option of working with a Western-owned partner. Outsourcing your manufacturing to a Western-owned company in China has the potential to offer numerous advantages, from increased quality control to reduced costs. In this blog post, we’ll look at why working with a Western-owned partner can be the key to leveling up your product manufacturing in China.
Why Culture Matters in China-Based Manufacturing Partnerships?
In the world of product manufacturing in China, understanding and respecting cultural nuances can make a significant difference in the success of your partnership. Culture matters in China-based manufacturing partnerships because it affects how business is conducted, communication is carried out, and decisions are made.
Cultural understanding also plays a vital role in negotiating and managing contracts in China. Chinese business practices often differ from those in Western countries, and it’s important to be aware of these differences. For example, Chinese culture emphasizes the concept of “guanxi,” which refers to the relationships and connections that are critical for business success. Understanding this concept and how it influences decision-making can help Western-owned partners navigate negotiations and establish mutually beneficial agreements.
In-Depth Industry Knowledge in the Chinese Market
Deep industry knowledge in the Chinese market is crucial for businesses aiming to succeed in manufacturing in China. One of the key advantages of working with a Western-owned partner is their in-depth knowledge and understanding of the Chinese manufacturing industry. They have the necessary expertise to navigate the complexities and nuances that often arise when dealing with Chinese manufacturers. This knowledge allows them to streamline the manufacturing process, ensuring efficiency and timely delivery of your products.
Intellectual Property Protection
Protecting your intellectual property (IP) is of utmost importance when manufacturing products in China, and working with a Western-owned partner can provide valuable safeguards in this regard. China has long been notorious for its lax IP protection laws, making it essential to partner with a company that understands and prioritizes the protection of your IP.
A Western-owned manufacturing partner brings a higher level of awareness and expertise when it comes to IP protection. They are more likely to have a comprehensive understanding of international IP laws and regulations, ensuring that your IP is respected and safeguarded throughout the manufacturing process. They can help you navigate the complexities of Chinese IP laws and provide guidance on the best practices to protect your patents, trademarks, and copyrights.
Supply Chain Transparency and Control
Working with a Western-owned partner ensures that you have full visibility and control over your supply chain. They have robust systems in place to provide real-time updates and reports on the progress of your manufacturing process. This means you can stay informed about every stage of production, from sourcing raw materials to final assembly. With this level of transparency, you can make well-informed decisions, identify and address any issues promptly, and maintain a seamless production flow.
Moreover, a Western-owned partner can help you maintain control over your supply chain by implementing stringent quality control measures. They understand the importance of consistent quality standards and will work closely with you to ensure that your products meet or exceed them. From conducting regular inspections to performing rigorous quality tests, they leave no room for compromise when it comes to the quality of your products.
Compliance and Ethical Standards
A Western-owned partner understands the importance of complying with local regulations and international standards. They have a strong grasp of the legal and regulatory landscape in China, ensuring that your products are manufactured in accordance with all applicable laws and regulations. This includes environmental regulations, labor standards, and product safety requirements. By working with a Western-owned partner, you can have confidence that your manufacturing process aligns with the necessary compliance measures.
Ethical standards are equally important, and a Western-owned partner can help you maintain the highest level of integrity. They are committed to conducting business ethically and responsibly, ensuring fair treatment of workers, responsible sourcing of materials, and transparency in business practices. They prioritize sustainability and social responsibility, minimizing the environmental impact and promoting positive social outcomes.
Cost Management
One of the key advantages of partnering with a Western-owned company is their expertise in cost control. They have extensive knowledge and experience in sourcing raw materials and negotiating with suppliers, allowing them to find the most cost-effective options for your manufacturing needs. By leveraging their network and industry connections, they can help you secure competitive prices for materials and components, reducing your overall production costs.
Additionally, a Western-owned partner can assist in streamlining the production process to increase efficiency and minimize waste. They have a thorough understanding of lean manufacturing principles and can implement strategies to reduce unnecessary expenses and optimize resource utilization. By identifying areas of improvement and implementing cost-saving measures, they can help you achieve greater profitability.
Maximizing Success with a Western-Owned Manufacturing Partner in China
When it comes to product manufacturing in China, partnering with a Western-owned company can greatly enhance your chances of success. The benefits of working with a Western-owned manufacturing partner in China are vast, and it all starts with maximizing your success.
Seeking a trustworthy and all-inclusive solution for product manufacturing services in China? Your search ends here with Shield Works. Established in 2020, we are proud to be a subsidiary of the esteemed C2W Group, a renowned manufacturing consultancy with a track record of delivering exceptional OEM manufacturing, supply chain management, quality control, and product development services since 2005.
With our team’s extensive 18 years of China-based manufacturing experience, Shield Works stands as a trustworthy and professional partner. We specialize in providing customized manufacturing and precision assembly activities exclusively for our Western client base. To ensure the utmost protection of your intellectual property rights, our production zones are dedicated to individual IPR safeguarding within our state-of-the-art Shield Works facility.
At Shield Works, we place paramount importance on delivering solutions that match your unique needs and standards. Our goal is to cater to businesses of all sizes, and we are committed to understanding your specific requirements to provide the best possible service.
Our highly skilled bilingual local team excels at providing tailored manufacturing solutions that match your unique needs and standards, ensuring that every aspect of your product will be meticulously crafted. We take pride in being your trusted manufacturing partner in the Far East. Take the first step in realizing your product’s potential by reaching out to us today. Let’s initiate a conversation about your product and explore how our expertise can be the catalyst for your success.
Practical Cost-Cutting Strategies When Manufacturing in China

In the dynamic landscape of global manufacturing, China has emerged as a dominant player, serving as a hub for companies seeking cost-effective production solutions. The allure of reduced labor costs, efficient supply chains, and access to a vast pool of skilled workers has drawn businesses from around the world to establish their manufacturing operations in the Middle Kingdom.
However, while manufacturing in China offers tremendous advantages, it also comes with its fair share of challenges. From navigating cultural nuances to coping with regulatory complexities, foreign companies must adopt a strategic approach to mitigate potential risks and maximize cost-saving opportunities.
This blog is your comprehensive guide to uncovering practical and effective cost-cutting strategies when manufacturing in China. We will delve into various tactics that can empower your business to optimize expenses without compromising product quality or supply chain reliability.
Analyze Your Expenses
The first step in implementing effective cost-saving measures for your business is to analyze your expenses thoroughly. By identifying the areas where you are overspending, you can create a solid plan to reduce unnecessary expenses and increase your profitability. This process requires a detailed review of your business expenses, including utilities, office rent, supplies, and salaries. By understanding where your money is going, you can make informed decisions about where to cut costs. Consider looking for any unnecessary expenses or areas of inefficiency that can be reduced or eliminated. With this approach, you can achieve significant cost savings without sacrificing quality or efficiency in your business operations.
Reduce Overhead Costs
Overhead costs can be a major drain on a company’s finances. These include expenses such as rent, utilities, and office supplies. To reduce these costs, consider downsizing to a smaller office space or implementing a remote work policy. Another option is to switch to energy-efficient appliances and lighting to lower utility bills. Take stock of your office supplies and purchase them in bulk to save money. Also, consider outsourcing certain tasks to freelancers instead of hiring full-time staff. Reducing overhead costs can significantly improve your bottom line without compromising productivity or quality.
Embrace Technology and Automation
Technology has become a game-changer for businesses in recent years, making it essential to embrace it as a cost-saving measure. Automation can help businesses save both time and money by streamlining processes and reducing the need for manual labor. From inventory management to payroll processing, businesses can leverage technology and automation to eliminate inefficiencies and cut down on costs. This can be achieved by adopting software solutions that help with data analysis, reporting, and other essential business operations. Additionally, businesses can consider investing in artificial intelligence and machine learning technologies that help automate tasks that were previously performed by employees. Embracing technology and automation is crucial in achieving long-term cost savings and enhancing efficiency.
Negotiate Better Deals with Suppliers and Vendors
As a business owner, it’s essential to establish strong relationships with your suppliers and vendors. These relationships can help you to secure better deals, which ultimately leads to cost savings for your business. To start, research and compare prices offered by different suppliers to identify opportunities for negotiation. Then, approach your current suppliers to discuss the possibility of a discount, or seek out new suppliers who are willing to provide better rates. Additionally, consider the option of bulk purchases, which may attract discounts. With effective negotiation, you can significantly reduce costs and improve profitability for your business.
Implement Energy-Saving Measures
Energy consumption is a major expense for most businesses. Implementing energy-saving measures can significantly reduce costs and help your organization become more eco-friendly. Start by assessing your energy usage patterns to identify areas where you can cut back. Some practical ways to conserve energy include replacing traditional light bulbs with LED ones, using motion sensors and timers to control lighting and HVAC systems, and investing in energy-efficient equipment. You could also consider switching to renewable energy sources such as solar or wind power. By implementing these energy-saving measures, you can not only reduce your costs but also improve your corporate social responsibility image.
Optimize Supply Chain
In a bid to reduce costs, companies need to prioritize supply chain optimization. This process involves scrutinizing the entire supply chain to identify potential inefficiencies and eliminate them. By optimizing the supply chain, businesses can enhance efficiency, speed up processes, and reduce costs.
One way of optimizing the supply chain is by identifying redundant processes. This involves streamlining supply chain procedures to eliminate wastage, duplication, and inefficiencies. Companies can also consider switching to a more efficient transportation method that can help reduce transportation costs and boost delivery times.
Another important aspect of supply chain optimization is ensuring proper inventory management. By accurately predicting customer demand and ensuring timely restocking, businesses can reduce storage costs, minimize inventory holding costs, and ensure better cash flow.
Work With a Western-owned Manufacturing Company in China
In conclusion, when manufacturing in China, businesses need to implement practical cost-cutting strategies to stay competitive in the global market. China’s reputation as the “world’s factory” offers numerous advantages, but it also comes with certain challenges that can impact production costs. By adopting a well-thought-out approach and leveraging various cost-cutting techniques, companies can navigate these challenges and optimize their manufacturing operations.
Considering partnering with a reputable manufacturing company in China? Look no further than Shield Works. We are an exceptional choice, distinguished by our British ownership and management. Our core expertise lies in providing premium contract manufacturing and product assembly services. Our team of seasoned professionals is dedicated to crafting bespoke solutions tailored to meet the needs of businesses, regardless of their scale. Don’t hesitate to reach out today and see what value we can bring to your journey!
Supply Chain Networks: Why Does Manufacturing in China Still Work?

Whether you’re outsourcing your production to China or not, there is no denying that manufacturing in China is one of the best options for many overseas companies.
China has maintained its position as the world’s largest manufacturing hub for the past 12 consecutive years.
There are many reasons why manufacturing in China still works.
Let’s dig a little deeper into why.
Does China Still Have Cost Advantages?
In the past decades, we have witnessed the rapid growth of China’s development. Most believed that it was the cost advantage and human resources that made China succeed.
Maybe it was, but things have changed.
Nowadays, China’s average labor costs aren’t low compared to many southeast Asian nations, such as Vietnam, Malaysia and the Philippines. The wages of skilled workers and high-teach talents grow fairly fast. Also, the average land prices are rapidly rising.
Therefore, there are many concerns that overseas companies tend to move their production to lower-cost countries since labor costs and land prices are getting higher in China.
However, it’s reported that foreign direct investment (FDI) topped 1 trillion RMB in 2021. It’s pretty clear that the comprehensive strength of China as a manufacturing superpower shouldn’t be neglected.
The answer is that China’s supply chain system is far more advanced than any other in the world.
Products Sold Worldwide Are Manufactured In China
You may have heard that in China, there are some small cities or even small towns
that are inconspicuous making world-class manufacturing contributions.
For example, Huludao, a coastal city in the Northeast China’s Liaoning province, is producing 25% of swimsuits in the global market. Since 2011, Huludao has been hosting an international beach-swimwear culture expo to expand its businesses and brands internationally.
In Yucheng County, located in Henan Province, more than 1,200 measuring tape making companies whose combined annual output exceeds 1.5 billion steel measuring tapes, accounting for 85% in China and 60% around the world.
So, you may wonder how such industries without high technology or difficult designs find their business opportunities.
By relying on China’s supply chain system, manufacturing in China will be more efficient, helping many businesses from home and abroad are able to gain their footholds.
The Problem Between Efficiency & Flexibility
Simply put, imagine that you want to outsource your production to a factory in China, there is no doubt that you will choose a high-efficiency factory to work with.
But keep in mind that only by being more specialized can a factory improve efficiency. In this case, it’s not hard to imagine this factory will be locked in certain product lines.
In this case, if you want something to be changed quickly, this factory will not be able to satisfy your needs and maybe you will turn to someone new. So, you also want the factory to be flexible. But flexibility is an obstacle to becoming a specialization.
Now you can see that keeping high efficiency and flexibility may not be compatible at the same time in a normal factory.
How Do Supply Chain Networks Work?
However, things will be much different if there is a powerful supply chain network.
Now there are tons of small and medium businesses (aka SMBs) that are ready to produce only some basic parts. And these SEBs are specialized in their field. Only in this way can these factories improve their efficiency without sacrificing much time and resources. Each SMB produces the basic elements, and every part can be easily assembled in another factory.
Then, all the SMBs get connected to be a wide supply chain network, solving the flexibility problem. In the end, these SMBs in the towns or the cities make themselves the certain type of manufacturing clusters.
It’s like Lego construction. Different factories produce different specific shapes of blocks with high efficiency. When you need some certain shape of blocks, you can purchase whatever you need and get them assembled, building your products.
The supply chain network connects businesses, making it easier for you to gather information and build your enterprise.
More importantly, the whole network nurtures an ability to control costs, which makes it hard for lower labor costs and land prices hard to contend with.
Let Shield Works Be Your Custom Manufacturing Partner
If are moving your production to China and looking for a reliable manufacturing partner, look no further. We are glad to help.
Shield Works is a British owned and managed company providing customized OEM manufacturing and assembly activities. Contact us to discuss your project today.