Boosting Efficiency: Top 5 Strategies to Enhance Your Manufacturing Competitiveness

In today’s competitive landscape, manufacturing companies are continually pressed to enhance their efficiency and productivity. Staying ahead requires not just keeping up with industry trends, but setting the pace. One effective way to boost manufacturing competitiveness is by tapping into the vast resources offered by manufacturing in China. By finding a manufacturer in China, companies can access a wide range of cost-effective solutions and take advantage of the country’s expertise in various industries.
Embrace Technological Advancements
The integration of cutting-edge technologies, including automation, robotics, and artificial intelligence (AI), into manufacturing processes can significantly elevate efficiency and output. These advancements empower manufacturers to not only expedite production timelines but also ensure the consistent delivery of superior-quality products.
One of the transformative impacts of embracing technological advancements is the remarkable reduction in downtime. Automated systems and robotics are designed for continuous operation, drastically reducing the likelihood of production halts that are common with manual processes. Moreover, AI-driven predictive maintenance can foresee equipment failures before they occur, allowing for preemptive repairs that further minimize downtime.
Lean Manufacturing Principles
Lean Manufacturing Principles are all about doing more with less. This methodological approach towards manufacturing zeroes in on cutting out unnecessary processes, reducing waste, and making operations more agile. It’s a systematic method to streamline both the production and administrative aspects of manufacturing to boost efficiency and ensure a smoother workflow. By scrutinizing every step of the production process and eliminating non-value-adding activities, companies can significantly reduce costs and enhance product value for the consumer.
Central to implementing lean manufacturing is the concept of continuous improvement or Kaizen. This principle encourages a culture where employees at all levels are actively looking for ways to improve processes, which can lead to significant enhancements over time. This mindset not only increases productivity but also fosters a more engaged and motivated workforce.
Strengthen Supply Chain Resilience
Enhancing supply chain resilience involves strategic planning and proactive management to mitigate risks and adapt swiftly to disruptions. A key strategy is the diversification of the supplier base. By not relying on a single source for materials or components, you can reduce the risk of crippling shortages and maintain steady production flows even when certain segments of the supply chain are under stress.
Building strong, transparent relationships with suppliers is also paramount. Effective communication channels enable real-time monitoring and quick responses to potential supply chain issues. This collaborative approach fosters mutual understanding and facilitates the development of contingency plans, ensuring both parties can navigate challenges more effectively.
Focus on Quality and Compliance
High-quality products that meet or exceed regulatory standards can significantly elevate a manufacturer’s market position, creating a strong brand identity synonymous with trust and reliability. This commitment to quality and compliance can set a manufacturer apart in a crowded market, attracting a loyal customer base and fostering long-term business growth.
To achieve this, you have to conduct quality control and regulatory compliance in every facet of your production in China. This involves pre-production audits and reviews of manufacturing processes to ensure they align with both internal quality benchmarks and external regulatory requirements. By implementing comprehensive quality management systems, you can proactively identify and rectify potential issues before they escalate, ensuring that the end products not only meet but surpass customer expectations.
Cultivate Skilled Workforce
Investing in the continuous training and development of employees is a cornerstone strategy for manufacturers aiming to bolster their competitiveness. Such an investment not only equips the workforce with the necessary skills to operate advanced machinery and adopt innovative manufacturing processes but also fosters a culture of continuous improvement and adaptability.
Moreover, fostering a skilled workforce extends beyond traditional training programs. It involves actively engaging employees in problem-solving and decision-making processes, thereby empowering them. Such engagement not only enhances their skill set but also boosts morale and loyalty, as employees feel more vested in the company’s success.
Key Considerations When Manufacturing in China
Manufacturing in China can offer many advantages, including cost reductions, access to a vast market, and a developed supply chain. However, several key considerations need to be kept in mind to ensure success and compliance with relevant standards and regulations. Here are some important aspects to consider when manufacturing in China:
1. Quality Control
Quality control is crucial when manufacturing products in China. Establishing rigorous quality assurance processes is essential to ensure that products meet the required standards and specifications. Regular on-site inspections and audits, as well as partnering with reputable factories that have a proven track record, are ways to maintain high standards.
2. Intellectual Property Protection
Intellectual property (IP) rights are a significant concern for businesses manufacturing abroad. In China, it’s vital to register your IP (patents, trademarks, and designs) locally since China operates on a first-to-file basis rather than first-to-use. Taking proactive measures such as working with local legal experts to navigate the IP landscape and implementing confidentiality agreements is advisable.
3. Regulatory Compliance
Navigating the regulatory environment in China is complex due to the country’s stringent and often changing regulations. Compliance with both local and international laws is crucial. This includes understanding the requirements for certifications and standards for exported goods. Partnering with local experts or consulting firms can help navigate these complexities.
4. Cultural Understanding and Communication
Cultural differences can impact business operations significantly. Understanding local business practices, negotiation styles, and the language barrier is essential. Building strong relationships with local partners and possibly hiring local staff or consultants who understand the business culture can be very beneficial.
5. Local Partnerships
Choose partners who have a track record in your industry and whose business goals align with yours. Compatibility in business culture and work ethics is essential for long-term cooperation. If you’re looking for a company that has all your manufacturing needs covered, look no further than Shield Works. As a British-owned and managed company, we specialize in contract manufacturing and product assembly services. We employ a team of skilled professionals who are experts in their respective fields, enabling us to tackle even the most complex projects with precision and efficiency. Our state-of-the-art facilities are equipped with the latest technology and machinery, ensuring that we meet our client’s requirements with the highest levels of quality and on-time delivery. To discuss your manufacturing needs and how we can support your business goals, please contact us today. We look forward to partnering with you to achieve outstanding results.
Understanding the Differences: Industrial Design vs. Product Design

When considering a career or business in the world of design, it’s crucial to understand the differences between industrial design and product design. While these terms are often used interchangeably, they actually represent distinct disciplines with unique objectives and outcomes. In this blog post, we will explore the nuances of industrial design and product design, helping you determine which path aligns best with your goals.
Understanding the Core of Industrial Design
At its essence, industrial design merges art with engineering to enhance the physical experience of products. This discipline emphasizes the creation of designs that balance aesthetic appeal with ergonomic functionality, ensuring that products are not only attractive but also comfortable and practical for the user.
Industrial designers are involved in the intricacy of product development, from the initial sketches to the final production details, focusing on aspects such as material selection, color, shape, and texture. They apply their understanding of how people use products to improve the usability and desirability of a wide variety of items, including everything from kitchen gadgets to personal electronics.
The Fundamentals of Product Design Explained
Product design involves a holistic approach to creating a product, considering every stage from the initial idea to its introduction to the market. This discipline integrates a blend of user experience, technical feasibility, and market viability to develop products that meet the end-users’ needs while achieving business goals. At the core of product design is the problem-solving process, where designers assess user needs, market gaps, and potential technological solutions to craft products that are both innovative and functional.
In this realm, designers navigate through complex challenges, including understanding the competitive landscape, adhering to budget constraints, and ensuring the sustainability of the design. Their work is enriched by a multidisciplinary collaboration, drawing insights from fields such as engineering, marketing, and user interface design to ensure the product resonates with its intended audience.
Key Differences Between Industrial and Product Design
Industrial design and product design are closely related fields, but they have distinct focuses and methodologies. Here are the key differences between the two:
Focus and Scope
Industrial design is primarily concerned with the physical aspects of a product and its interaction with users. It often involves creating a design that can be repeatedly manufactured. Product design covers a broader scope, including the ideation, planning, and implementation of a product, focusing more on the solution rather than just the physical form.
End Goals
The main goal of industrial design is to improve product aesthetics and usability to drive consumer interest and satisfaction. Product design aims to solve specific user problems, often prioritizing function and feasibility over form.
Processes Involved
While both fields involve research and prototyping, industrial design leans more towards artistic conceptualization and user-centric evaluation. Product design integrates more direct problem-solving processes, often requiring rigorous testing of product functionality against user requirements.
Outcome Expectations
Industrial designers are expected to deliver designs that are not only innovative but also viable and manufacturable. Product designers are tasked with ensuring the product functions seamlessly and meets the market demands efficiently.
Interdisciplinary Interaction
Industrial designers frequently collaborate with engineers and marketers to refine product designs for manufacturability and market appeal. Product designers often work closely with business strategists, UX/UI designers, and data analysts to align the product’s functionality with business goals and user expectations.
Where Industrial and Product Design Overlap
In the space where industrial and product design converge, a synergy emerges that encapsulates the best of both worlds. This intersection is characterized by a shared dedication to understanding and enhancing user experience, a common thread that runs through both fields. Designers in both arenas employ a methodology that emphasizes creativity and innovation, fueled by an acute awareness of user needs and the desire to fulfill them in the most efficient and aesthetically pleasing manner possible.
Collaboration between industrial and product designers often leads to the creation of products that are not just visually appealing but are also intuitively functional, seamlessly integrating into the lives of users. This partnership capitalizes on the strengths of each discipline: the artistic and ergonomic focus of industrial design melds with the strategic and holistic perspective of product design. Together, they tackle complex design challenges, from conceptualization through to product launch, ensuring that every aspect of the user’s interaction with the product is considered and optimized.
Industrial Design vs Product Design: Which Fits Your Goals?
Both industrial and product design are integral to the successful development of new products, each with its unique focus and methods. By understanding the differences and intersections between these two fields, you can better strategize the design processes and choose the right expertise for your project needs.
Interested in harnessing the power of expert design for your next project?
Partnering with a reliable and experienced company like Shield Works, known for our high-quality contract manufacturing and product development services, can significantly enhance your operations. As a British-owned and managed company, we ensure stringent quality control and consistent delivery. Contact us today to see how our tailored design services can bring your vision to life, ensuring both aesthetic appeal and functional excellence.
How to Ensure Transparent Communication with a Contract Manufacturer in China?

Working with a contract manufacturer in China can be a highly beneficial business decision, offering cost-effective production solutions and access to specialized expertise. However, the distance and potential cultural differences between you and your manufacturing partner can sometimes pose challenges to effective communication. In order to ensure a successful partnership with your contract manufacturer in China, it is crucial to prioritize transparent communication. By implementing key strategies and best practices, you can establish clear channels of communication and build a strong foundation for a long-lasting relationship.
The Role of Transparency in Building Trust
Transparency plays a crucial role in building trust with contract manufacturers in China, or anywhere else for that matter. Trust is the cornerstone of any successful business relationship, especially in complex and often opaque supply chains.
1. Clarity in Communication
Transparent communication ensures that all parties are on the same page regarding expectations, product specifications, timelines, and pricing. When both parties clearly understand their responsibilities, it reduces the risk of misunderstandings and conflicts. Regular updates and open lines of communication also facilitate quicker resolutions to any issues that may arise.
2. Quality Assurance
Sharing detailed information about manufacturing processes, quality control measures, and compliance with standards is crucial. Transparent reporting on these aspects reassures clients about the quality of the final product. Additionally, allowing audits and visits to manufacturing facilities can further boost confidence in the manufacturing processes.
3. Regulatory Compliance
In industries where regulatory compliance is critical, transparency is essential. Sharing detailed documentation and updates on compliance with local and international laws builds trust. It ensures that the products are manufactured under lawful conditions, which is especially important in markets that are sensitive to regulatory compliance like pharmaceuticals, food, and electronics.
Establishing Clear Communication Channels
To create a foundation for successful collaboration with your contract manufacturer in China, it’s essential to pinpoint and utilize the most effective communication tools available. From the outset, delineate all project expectations, roles, and timelines to prevent any ambiguity. Leveraging various technologies, such as emails, phone conversations, and video conferencing platforms, enables consistent interaction and ensures both parties remain informed throughout the production cycle. Implementing a structured schedule for updates and progress reports can significantly enhance this dynamic, keeping both you and your manufacturing partner aligned on every aspect of the project.
Moreover, integrating a shared project management tool or platform can serve as a central repository for all relevant documents, updates, and communications. This not only streamlines the flow of information but also provides a transparent record of interactions, decisions, and modifications made during the course of the partnership. It’s beneficial to agree on a primary method of communication for urgent matters to ensure swift responses and decision-making.
Another critical step is agreeing on a common language for all formal documentation and communication, which can help minimize misunderstandings and provide clarity. While English is often the lingua franca in international business, ensuring all key documents are available in both English and Chinese can cater to the comfort levels of all involved, promoting better understanding and efficiency.
Regular Updates and Scheduled Meetings
To cultivate a flourishing partnership with your contract manufacturer in China, establishing a routine for updates and scheduled meetings is vital. This structured approach facilitates ongoing dialogue, enabling you and your manufacturing partner to stay closely connected regarding the project’s status, challenges, and advancements.
Implement a system for periodic updates that may include weekly or bi-weekly check-ins, depending on the project’s complexity and duration. These check-ins can be conducted via your agreed-upon communication platforms, ensuring that both parties are consistently informed and engaged.
Scheduled meetings, on the other hand, should be more comprehensive and focused on reviewing project milestones, discussing strategic adjustments if necessary, and planning for upcoming phases. These sessions offer a dedicated time to delve deeper into discussions that require more attention and cannot be fully addressed in brief updates.
It’s also prudent to have a flexible meeting schedule that respects the time zones of all participants, ensuring that meetings are held at times convenient for both you and your Chinese manufacturing partner. This consideration demonstrates respect for your partner’s time and contributes to a more productive and
Building Trust Through Transparency and Patience
In fostering a relationship with your contract manufacturer in China, transparency serves as the bedrock upon which trust is built. Openly sharing your expectations, needs, and potential obstacles sets the stage for a transparent dialogue, crucial for a harmonious partnership. It ensures that both parties are on the same page, reducing the likelihood of misunderstandings and fostering mutual respect. Additionally, adopting a patient stance is invaluable. Given the nuances of navigating cross-cultural communications, allowing extra time for clarification and understanding can mitigate frustrations on both sides. This patience demonstrates respect for the process and acknowledges the effort required to bridge the linguistic and cultural divide. Embracing these principles of transparency and patience not only solidifies the foundation of your partnership but also propels the collaboration towards achieving shared goals, creating a pathway to a durable and mutually beneficial relationship.
Transparent communication is not merely about exchanging information; it’s about building a partnership based on trust and mutual respect. For more information about contract manufacturing in China, feel free to contact us. We are here to help you optimize your supply chain and achieve success in your manufacturing goals.
The Comprehensive Guide to Developing Electronic Products in China
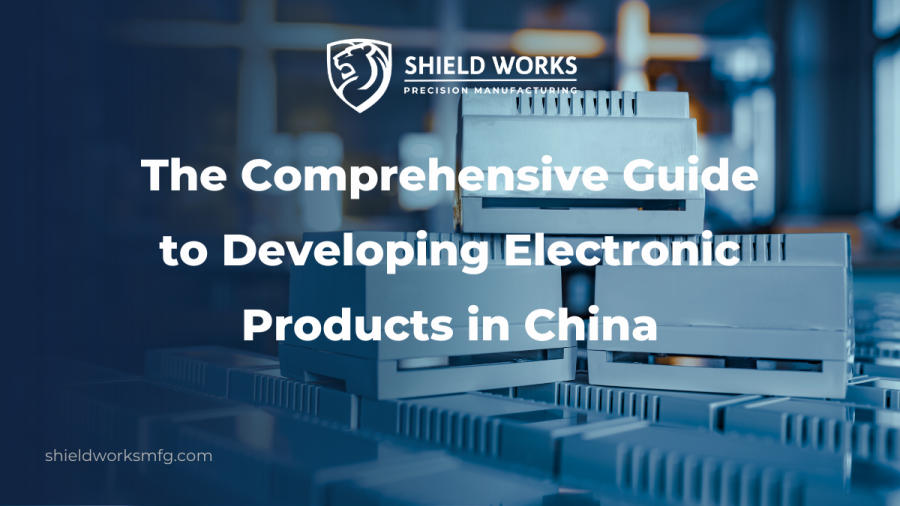
China has long been the global hub for electronic product development, boasting unmatched manufacturing capabilities, advanced technology infrastructure, and cost-efficient production. For entrepreneurs and businesses looking to develop electronic products, China offers a comprehensive ecosystem to turn innovative ideas into market-ready products. This guide will walk you through the essential steps of developing electronic products in China, highlighting the benefits, challenges, and expert tips to ensure your project’s success.
The Electronics Manufacturing Ecosystem in China
The electronics manufacturing ecosystem in China is a dynamic and intricate network, consisting of a wide range of suppliers, manufacturers, and service providers. At its core, this ecosystem is designed to facilitate the efficient production of electronic goods, from small components to complex devices. For businesses aiming to tap into this market, comprehending the ecosystem’s structure is imperative. This involves not just knowing where to find reliable component suppliers but also understanding the role of assembly plants, testing facilities, and packaging companies in the broader manufacturing process.
The Key Steps Involved in the Electronic Development Process
Embarking on the electronic manufacturing and development process necessitates a methodical approach that spans several critical stages.
Start by understanding the demand for your product and analyzing both competitors and potential customers. Once you have a clear product idea, proceed to the design and prototyping phase. Collaborate with experienced industrial designers and engineers who can translate your vision into a functional design.
Choosing the right manufacturing partner is crucial for the success of your electronic product. Look for manufacturers with a proven track record in producing similar products. It’s advisable to visit the factory in person or hire a local representative to conduct thorough due diligence. Work closely with your supplier to create a product prototype, allowing you to better understand your concept and make necessary adjustments.
Next, conduct a small production run to test the manufacturing process and identify any issues. If everything goes well, you can confidently begin full-scale production.
Top 5 Hubs for Electronic Products in China
China is a global leader in electronics manufacturing, and several cities have developed into major hubs for various aspects of the industry. Here are the top five hubs for electronic products in China and their specific focuses:
1. Shenzhen
Shenzhen is often referred to as the “Silicon Valley of Hardware.” It is the heart of China’s electronics industry, known for its vast electronics markets, high-tech manufacturing capabilities, and numerous tech startups. The city is home to major companies like Huawei, DJI, and ZTE. Shenzhen’s ecosystem supports everything from prototyping to mass production.
2. Shanghai
Shanghai is a key player in the semiconductor industry, with a strong focus on R&D and high-end manufacturing. The city hosts several major semiconductor companies and research institutes. It is also a center for integrated circuits (IC) design and production, making it crucial for the development of advanced electronics.
3. Beijing
Beijing is a major hub for telecommunications and software development. It houses the headquarters of leading telecom companies like China Mobile and China Unicom. The city is also a center for artificial intelligence research and development, with many tech giants and startups working on AI technologies.
4. Suzhou
Suzhou, particularly its Suzhou Industrial Park, is known for precision manufacturing and the production of high-quality electronic components. The city attracts significant foreign investment and is home to many multinational corporations specializing in electronics assembly and component manufacturing.
5. Guangzhou
Guangzhou is a major manufacturing base for home appliances and consumer electronics. The city is known for producing a wide range of products, including air conditioners, refrigerators, and televisions. Guangzhou’s electronics industry benefits from its strategic location and extensive logistics network.
Consideration when Developing Electronic Products in China
When venturing into electronic manufacturing in China, several factors must be considered to ensure success:
1. Navigating Intellectual Property Concerns
In the competitive realm of developing electronic products in China, safeguarding your intellectual property (IP) stands as a paramount concern. To effectively protect your inventions and ideas, it’s essential to have a comprehensive understanding of the IP landscape within the country. Engaging with experienced legal professionals who specialize in Chinese IP law is a critical step. These experts can assist in the drafting and registration of patents and trademarks tailored to the Chinese market’s unique requirements. They play a crucial role in crafting confidentiality agreements that are robust and enforceable under local laws.
2. Adapting to Regulatory Requirements and Standards
Ensuring compliance with China’s regulatory landscape is a cornerstone of launching successful electronic products in the market. China has a detailed framework of standards and certifications specific to the electronics industry, including but not limited to the CCC (China Compulsory Certificate) for safety and quality, and environmental directives similar to RoHS (Restriction of Hazardous Substances). Navigating this landscape requires a detailed understanding of the pertinent regulations that apply to your product, which can vary widely depending on its specific features and functionalities.
3. Managing Supply Chain and Logistics
In the realm of electronic product development in China, the ability to streamline and effectively manage your supply chain and logistics operations is indispensable. Collaborating closely with your manufacturing partners to fine-tune supply chain operations ensures that you can navigate the complexities of sourcing materials, managing inventory, and maintaining a seamless production schedule. Implementing strategies to reduce lead times and mitigate costs without compromising quality is critical.
Work with A Reliable Manufacturing Partner
Selecting the appropriate manufacturing partner is critical in the journey of bringing an electronic product to life. This decision can significantly impact the quality, timing, and overall success of your project. Initiating this process requires conducting comprehensive research to filter through the vast number of manufacturers in China. A diligent approach includes evaluating their experience, production capacity, and specialization in the electronics sector.
Visiting potential manufacturing facilities is an invaluable step, providing direct insight into their operational capabilities and work culture. Such visits also allow for the assessment of their quality control processes and the ability to meet large-scale production demands efficiently. Requesting references and case studies from previous clients give a clearer picture of the manufacturer’s reliability and expertise in handling projects similar to yours.
Additionally, it’s crucial to assess the manufacturer’s communication practices and responsiveness, as these factors can significantly influence the smooth progression of your product development cycle. Ensuring that your manufacturing partner understands your project’s specific requirements and can offer constructive feedback and solutions is essential for a fruitful collaboration.
If you are seeking a reliable and experienced manufacturing company, look further than Shield Works. We excel in delivering high-quality contract manufacturing and assembly services, designed to boost your operational efficiency. As a British-owned and managed company, we guarantee stringent quality control and consistent delivery. Contact us today to discover how we can make your investment count.
5 Key Strategies to Minimize Lead Time when Manufacturing in China

When manufacturing in China, optimizing production and delivery processes is crucial for business success. Among these, one of the most pivotal yet sometimes neglected metrics is “Lead Time.” The lead time directly impacts your competitiveness and customer satisfaction. Reducing lead time is paramount because it enhances your ability to meet customer demands swiftly and outpace competitors. A shorter lead time means quicker responsiveness to market changes, reduced inventory costs, improved cash flow, and ultimately, higher customer satisfaction. This article will delve into what lead time is, why it matters, and how you can improve it to ensure your business remains competitive and responsive.
What is Lead Time?
Lead time is the total time it takes for a product to be made available to the customer after the initial order is placed. This includes the entire cycle from processing the order, sourcing materials, manufacturing, and shipping the product to the end-user. Lead time can vary greatly depending on the nature of the product, the efficiency of the supply chain, and the manufacturing processes involved.
Understanding and managing lead time is crucial because it directly impacts your inventory levels, customer satisfaction, and overall business efficiency. Long lead times can result in stock shortages, increased holding costs, and dissatisfied customers, while shorter lead times can enhance customer satisfaction and competitive advantage.
Why Product Lead Time Matters More Than Ever?
In the digital age, where instant gratification has become the norm, customers’ expectations for rapid delivery times have escalated, making the optimization of product lead time a paramount concern for businesses. This urgency is particularly pronounced in the realm of e-commerce, where the ability to quickly fulfill orders can be the deciding factor in capturing or losing a sale. The acceleration of market dynamics and the intensification of global competition mean that companies can no longer afford the luxury of lengthy lead times without facing significant repercussions.
Analyzing the Impact of Long Lead Times on Your Business
Extended lead times can severely disrupt the operational flow of your business, leading to a cascade of unfavorable outcomes. Among these are the risks of experiencing stock shortages or, conversely, accumulating excessive inventory that ties up valuable resources. Such situations elevate the carrying costs, directly impacting your bottom line. Moreover, the inability to swiftly meet market demands can result in missed sales opportunities, as customers may turn to competitors who offer faster delivery times. This lag can also stifle your ability to adapt to consumer preferences, putting your business at risk of falling behind in a constantly evolving market. The repercussions extend beyond operational inefficiencies; long lead times can erode customer loyalty and satisfaction. In today’s fast-paced market, consumers have grown to expect quick and reliable service. When businesses fail to meet these expectations due to prolonged lead times, it not only leads to immediate dissatisfaction but can also harm long-term customer relationships. Addressing these challenges is crucial for maintaining a competitive edge and ensuring customer retention in the competitive landscape of Chinese manufacturing.
5 Key Strategies to Reduce Lead Time
Optimizing product lead time is vital for maintaining a competitive edge, particularly in the context of manufacturing in China. A strategic approach to streamlining this aspect involves several actionable steps
1. Optimize Your Supply Chain
Analyzing and optimizing each component of your supply chain is paramount. This includes selecting reliable suppliers who can provide materials quicker and more reliably, improving logistics for faster delivery, and using technology to streamline order processing and inventory management.
2. Implement Lean Manufacturing Principles
Lean manufacturing focuses on minimizing waste within manufacturing systems while simultaneously maximizing productivity. Techniques such as Just-In-Time (JIT) production can help reduce lead times by ensuring that the manufacturing process only occurs as needed, reducing the wait times and inventory levels.
3. Improve Forecasting Accuracy
Accurate demand forecasting helps you prepare for production in a more targeted way. Use historical data and market analysis to predict customer demand more accurately and plan your production schedule accordingly, which can significantly cut down on lead times.
4. Invest in Technology
Modern technologies like ERP (Enterprise Resource Planning) systems can integrate various processes from order taking to production and shipping. This integration helps in speeding up the process and reducing errors, which can otherwise extend the lead time.
5. Foster Strong Supplier Relationships
Developing strong relationships with your suppliers can lead to better and faster service. When suppliers are engaged and informed about your expectations and needs, they are more likely to prioritize your orders and work collaboratively to reduce lead times.
Boost Your Production Efficiency
Reducing product lead time is not just about speeding up production but optimizing every aspect of your production and delivery cycle. This strategic initiative demands ongoing refinement and the flexibility to respond swiftly to evolving market dynamics. By diligently implementing these strategies, you can achieve not only shortened lead times but also heightened operational efficiency and increased customer satisfaction levels.
Are you keen on discovering effective strategies to optimize your product lead time or seeking ways to significantly boost your operational efficiency? Contact us today! With almost 20 years of experience in China, we specialize in streamlining supply chain management and enhancing production processes. Our proven track record includes collaborating with diverse industries, from electronics to outdoor cookware, delivering tailored solutions that drive measurable results. Whether you’re aiming to reduce manufacturing cycles or improve inventory turnover, our dedicated team is ready to assist you every step of the way.
What to Know Before You Outsource Manufacturing for Your Company

Outsourcing manufacturing can revolutionize your business. It’s when you hire an external company to produce your goods, often leading to cost savings and increased efficiency. But jumping in without understanding the process can lead to serious issues like poor quality, supply chain hiccups, and unexpected expenses.
It’s crucial to get a clear picture before making any decisions. In this guide, we’ll break down what you need to know to outsource manufacturing effectively.
Read on for detailed insights that will help you navigate this critical business move with confidence.
Benefits of Outsourcing Manufacturing
Outsourcing manufacturing can be a game-changer for your business. It helps you cut costs, access advanced technology, focus on what you do best, and scale your operations efficiently. Let’s break down these benefits to see how they can help in growing your business.
Cost Savings
Outsourcing can save you a lot of money. You don’t need to invest in expensive equipment or facilities. External partners, often in cheaper regions, handle production for you. This way, you can use your money for other important parts of your business.
Access to Advanced Technology and Expertise
When you outsource, you get to use the latest technology without buying it yourself. Manufacturing partners have top-notch equipment and skilled workers. They know the best ways to make your products. This means better quality and fewer mistakes.
Focus on Core Business Activities
By letting someone else handle manufacturing, you can focus on what you do best. Spend more time on research, marketing, and customer service. This focus helps you improve your products and services. It also makes it easier to adapt to market changes.
Improved Efficiency and Scalability
Outsourcing makes your business more efficient. Manufacturing partners have smooth processes for production and shipping. This means faster production and delivery times. Plus, you can easily scale up or down depending on demand. This flexibility helps you manage resources better and stay profitable.
In short, outsourcing manufacturing offers big benefits. It saves money, gives you access to advanced tech, lets you focus on your strengths, and improves efficiency. Understanding these advantages can help you grow your business successfully.
Types of Manufacturing Services
When you decide to outsource manufacturing, it’s essential to understand the different types of manufacturing services available. Each type has unique benefits and applications. Here’s a look at some common manufacturing services you might consider.
Precision Assembly
Precision assembly involves putting together small, complex components with great accuracy. This service is vital for industries like electronics, aerospace, and medical devices, where even minor errors can cause significant issues.
Benefits and Applications
Precision assembly ensures high-quality and reliable products, meeting strict industry standards. It’s particularly useful in producing intricate devices that require exact specifications and consistency.
Custom Manufacturing
Custom manufacturing is about creating products that meet specific requirements. This service is perfect for businesses with unique needs or those looking to stand out in the market.
Tailored Solutions for Unique Products
Whether it’s a new product design or a specialized component, custom manufacturing offers tailored solutions that fit your exact specifications. It allows for flexibility in design and materials, enabling you to innovate and bring unique products to market.
Mass Production
Mass production focuses on producing large quantities of a product at a lower cost per unit. This service is ideal for businesses that need to manufacture items in bulk.
Economies of Scale
By producing more units, you can reduce the overall production cost, making it more economical. Mass production benefits industries like consumer goods, automotive, and food processing, where consistent, high-volume output is crucial.
Component Manufacturing
Component manufacturing involves creating specific parts that will be used in larger assemblies. This service is crucial for industries that require specialized components, such as automotive, electronics, and machinery.
Specialized Parts and Components
By outsourcing component manufacturing, businesses can focus on assembling the final product. It ensures that each part meets high-quality standards and works seamlessly with other components.
In summary, understanding the various types of manufacturing services helps you choose the right option for your business needs. Whether you need precise assembly, custom solutions, mass production, or specialized components, each service offers distinct advantages. These can enhance your manufacturing strategy and contribute to your business growth.
How to Choose the Right Manufacturing Partner
Selecting the right manufacturing partner is crucial for the success of your business. A good partner can ensure high-quality production, cost savings, and reliable delivery. Here are some key criteria to consider when you decide to outsource manufacturing.
Key Criteria: Quality Control, Cost, Communication, and Reliability
When choosing a manufacturing partner, quality control is paramount. Ensure they have strict quality assurance processes in place. Poor quality can lead to product failures and damage your brand’s reputation.
Cost is another critical factor. Compare the pricing structures of different partners, but don’t compromise on quality for the sake of saving money. Balance cost-effectiveness with quality to get the best value.
Effective communication is essential for a smooth partnership. Your manufacturing partner should be responsive and easy to communicate with. Clear communication helps in quickly resolving any issues that may arise.
Reliability is about consistent performance. Check if the partner has a track record of meeting deadlines and delivering products as promised. Reliability ensures that your production schedule stays on track.
Importance of Visiting Potential Partners
Visiting potential partners can give you a better understanding of their operations. You can see firsthand how they manage production, quality control, and their work environment. A visit also allows you to build a personal relationship with the partner, fostering trust and better cooperation.
Checking References and Past Work
Always check references and review the past work of potential manufacturing partners. Talking to their previous clients can provide insights into their reliability, quality of work, and professionalism.
Reviewing their past projects can help you assess if they have experience in manufacturing products similar to yours.
Choosing the right partner to outsource manufacturing involves evaluating quality control, cost, communication, and reliability. Visiting potential partners and checking their references and past work are essential steps in making an informed decision.
With the right partner, you can ensure high-quality production and contribute to your business’s growth.
Understanding the Outsourcing Process
Outsourcing your manufacturing involves several key steps to ensure a smooth and efficient production process. Understanding these steps can help you manage the process better and achieve your business goals.
Initial Consultation and Needs Assessment
The outsourcing process begins with an initial consultation and needs assessment. This step involves discussing your requirements with the manufacturing partner. You’ll outline your product specifications, volume needs, and any special considerations.
This assessment helps the partner understand your business and tailor their services to meet your needs.
Prototype Development and Testing
Once the initial assessment is complete, the next step is prototype development and testing. The manufacturing partner will create a prototype of your product. This phase is crucial as it allows you to evaluate the design, functionality, and quality of the product before full-scale production begins.
Testing the prototype ensures that any issues are identified and resolved early in the process. This step helps in fine-tuning the product to meet your exact specifications and standards.
Production Planning and Execution
After the prototype is approved, the production planning and execution phase begins. This step involves scheduling the production runs, sourcing materials, and setting up the manufacturing processes. The manufacturing partner will create a detailed plan to ensure that production runs smoothly and on schedule.
During this phase, communication between you and the manufacturing partner is vital. Regular updates and progress reports help in managing expectations and ensuring that any potential issues are addressed promptly.
Quality Control Measures
Quality control is a critical part of outsourcing your manufacturing. The manufacturing partner should have robust quality control measures in place to ensure that every product meets your standards. This includes regular inspections, testing, and quality assurance processes throughout the production cycle.
By understanding the outsourcing process, from initial consultation to quality control, you can ensure a successful partnership and high-quality production. Proper management of these steps will lead to efficient manufacturing and contribute to your business growth.
Common Challenges and How to Overcome Them
Outsourcing your manufacturing can bring many benefits, but it also comes with its own set of challenges. Understanding these challenges and how to address them can help you manage the process more effectively.
Communication Barriers and Time Zone Differences
One major challenge is communication barriers, especially when your manufacturing partner is in a different country. Time zone differences can complicate communication, leading to delays and misunderstandings. To overcome this, use clear and simple language to avoid jargon.
Schedule regular meetings at times that work for both parties, and use technology like video conferencing and project management tools to keep the communication lines open.
Quality Assurance and Maintaining Standards
Maintaining high-quality standards can be difficult when you’re not directly overseeing the production process. Ensuring that your manufacturing partner adheres to your quality expectations is crucial. Start by setting clear quality standards and providing detailed specifications and benchmarks.
Conduct regular quality inspections and audits, either in-person or through a third-party service. Establish a feedback loop to promptly address any quality issues that arise.
Intellectual Property Protection
Protecting your intellectual property (IP) is a significant concern when outsourcing manufacturing. Unauthorized use or theft of your designs and ideas can harm your business. To mitigate this risk, use robust legal agreements to protect your IP rights. Choose trusted partners with a good track record of respecting IP.
Regularly monitor your partner’s adherence to IP agreements to ensure compliance.
Logistical Challenges and Shipping Delays
Logistical issues and shipping delays can disrupt your supply chain and affect your business operations. Managing these challenges is vital for smooth production. Plan ahead and factor in potential delays when scheduling production. Diversify your suppliers to reduce dependency on a single source, and utilize shipment tracking systems to monitor the status of your goods.
In conclusion, while outsourcing your manufacturing comes with challenges, addressing communication barriers, maintaining quality, protecting IP, and managing logistics can help you overcome these hurdles. By implementing these practical solutions, you can ensure a smoother and more efficient outsourcing process.
Legal and Regulatory Considerations
When outsourcing your manufacturing, it’s essential to navigate legal and regulatory requirements to avoid potential pitfalls. Understanding these aspects helps ensure smooth and compliant operations.
Understanding International Trade Laws and Regulations
Familiarize yourself with the international trade laws and regulations that apply to both your country and the manufacturing partner’s country. This knowledge helps prevent legal issues and ensures your products meet all necessary standards.
Contracts and Agreements with Manufacturing Partners
Draft clear and comprehensive contracts with your manufacturing partners. These agreements should outline expectations, responsibilities, timelines, and penalties for non-compliance. Solid contracts protect both parties and set a clear framework for the partnership.
Ensuring Compliance with Industry Standards
Make sure your manufacturing partner complies with industry standards and certifications relevant to your products. Regular audits and inspections can help verify compliance and maintain high-quality production.
Protecting Intellectual Property Rights
Protecting your intellectual property is crucial when working with external partners. Use legal agreements to safeguard your designs, patents, and trademarks. Regularly monitor and enforce these agreements to ensure your IP remains secure.
By understanding and addressing these legal and regulatory considerations, you can safeguard your business and maintain a successful manufacturing partnership.
Successfully Outsource Manufacturing
Choosing to outsource manufacturing can bring significant benefits like cost savings, access to advanced technology, and the ability to focus on core business activities. However, it’s crucial to thoroughly research and plan each step, from selecting the right partner to understanding the entire process.
By addressing common challenges such as communication barriers and ensuring quality control, you can achieve smoother operations.
For businesses looking to protect their IP and maintain transparency, Shield Works offers unique advantages like secure individual production zones and 24/7 live video feed access. Take informed steps for your business growth by leveraging these benefits.
Contact us at Shield Works to explore how our tailored solutions can meet your manufacturing needs.
A Beginner’s Guide to OEM Tools
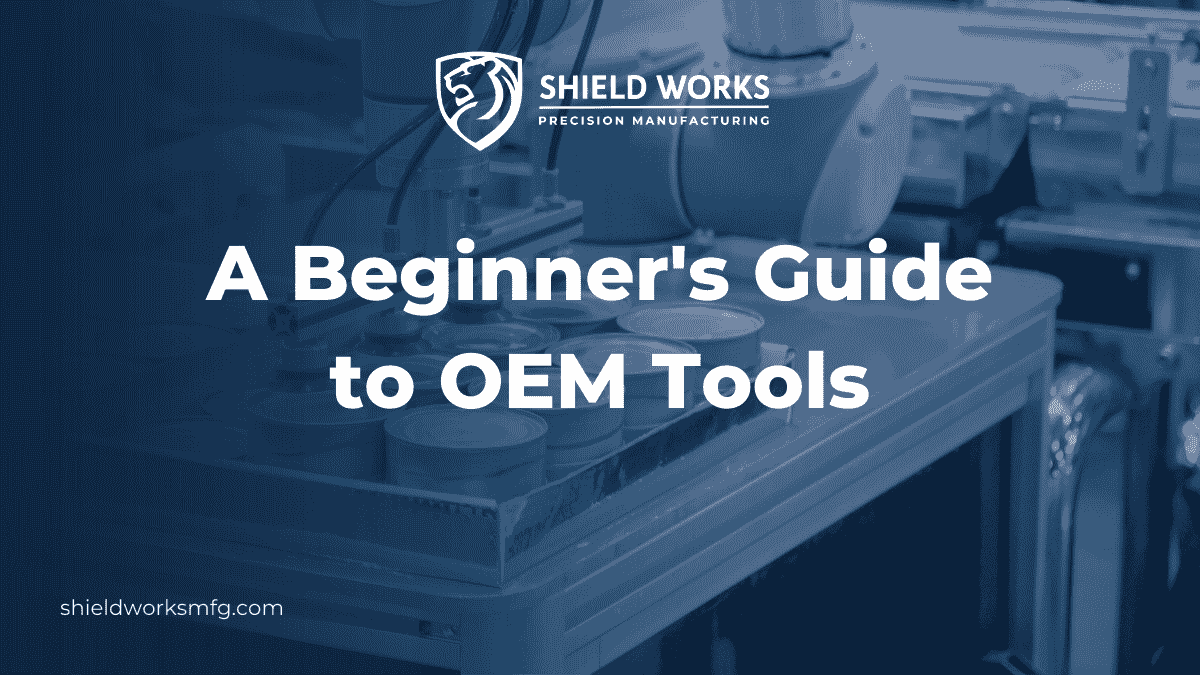
Have you wondered what drives the production of your favorite gadgets and vehicles? OEM tools have revolutionized the way we manufacture products, creating endless possibilities for innovation and efficiency.
These tools are the unsung heroes behind many of the high-quality products we use daily. Understanding these tools is key to staying ahead in the fast-paced world of manufacturing.
Imagine producing components that fit perfectly and function smoothly every time. That’s the power of OEM tools. They help create better products, leading to happier customers and fewer returns.
In this guide, we’ll dive into the exciting world of OEM tools and explore what you need to know to get started. Whether you’re new to manufacturing or looking to update your knowledge, this guide is your starting point. Let’s unlock the secrets of OEM tools together.
What Are OEM Tools?
OEM stands for Original Equipment Manufacturer. OEM tools are used in the production of parts and equipment that will be sold under another company’s brand. These tools are essential for creating high-quality, reliable products. They ensure that every component fits perfectly and functions smoothly.
Without OEM tools, the production process would be slower, less precise, and more prone to errors. This would lead to increased costs and lower-quality products.
OEM tools come in various forms, each designed for specific tasks. Some common types include:
- Stamping tools
- Cutting tools
- Injection molds
Stamping tools are used to cut or shape metal parts while cutting tools remove material to create the desired shape. Injection molds, on the other hand, are used in plastic manufacturing to produce parts with consistent quality.
These tools are critical in many industries, including:
- Automotive
- Aerospace
- Electronics
- Consumer goods
In the automotive industry, for example, stamping tools are used to create complex metal parts that must meet strict safety standards. In electronics, precision cutting tools are needed to manufacture small, intricate components.
Using OEM tools also helps manufacturers maintain high standards and produce goods that meet specific requirements. This results in better products and greater customer satisfaction. Furthermore, OEM tools allow for mass production without compromising quality, making it possible to meet the demands of a growing market.
Understanding OEM tools is essential for anyone involved in manufacturing. By using these tools effectively, manufacturers can improve their production processes, reduce costs, and deliver high-quality products that meet or exceed customer expectations.
Why OEM Tools Matter
OEM tools play a crucial role in product manufacturing. They ensure that every component fits perfectly and functions smoothly.
High-quality OEM tools lead to better products, which means happier customers and fewer returns. This is because OEM tools allow for precision and consistency in the manufacturing process.
The use of OEM tools helps reduce production time and costs, making manufacturing more efficient.
By speeding up the production process and minimizing errors, these tools help manufacturers save money and increase output. This efficiency is vital in competitive industries where time and cost savings can make a significant difference.
With the right OEM tools, manufacturers can achieve the precision needed for complex and detailed parts. This is especially important in industries like automotive, aerospace, and electronics, where even small deviations can lead to significant issues.
For example, in the automotive industry, the precise fitting of parts can affect the safety and performance of vehicles. In electronics, tiny components must fit perfectly to ensure the proper functioning of devices.
OEM tools also contribute to product innovation. As technology advances, the need for new and improved tools grows. This drives the development of cutting-edge OEM tools that can handle new materials and manufacturing techniques.
By staying up-to-date with the latest OEM tools, manufacturers can remain competitive and continue to meet the evolving demands of the market.
OEM Tool Options in Detail
OEM tools are diverse and specialized, each designed for specific tasks in various types of manufacturing processes. Understanding the various types of OEM tools can help manufacturers choose the right tools for their needs, ensuring precision, efficiency, and high-quality output.
In this section, we will explore the different types of OEM tools in detail, discussing their:
- Functions
- Applications
- Benefits
From stamping and cutting tools to injection molds and more advanced equipment, we will cover a broad range of tools essential for various manufacturing processes. So here they are in more detail:
Stamping Tools
Stamping tools are essential in industries requiring high precision and durability, such as automotive and aerospace. These tools cut, shape, or emboss metal sheets into desired forms using a process called stamping. The metal sheet is placed into a stamping press, where a tool and die surface form the metal into a new shape.
There are various types of stamping tools, including dies, presses, and punches. Dies cut or shape material, while presses exert high pressure to form the metal. Single-station dies perform one operation, and progressive dies perform multiple operations in a single cycle.
Stamping tools can produce complex shapes quickly and accurately, crucial for automotive parts like body panels and chassis components. In the aerospace sector, stamping tools create parts that require exceptional strength and precision, using metals like aluminum, steel, and titanium.
Overall, stamping tools provide high precision, durability, and efficiency. By investing in quality tools and proper maintenance, manufacturers can achieve consistent, high-quality results.
Cutting Tools
Cutting tools are vital in manufacturing, designed to remove material from a workpiece to create the desired shape and size. These tools come in various forms, including:
- Drills
- Saws
- Milling cutters
They are essential for processes that require high precision and fine detail, such as electronics manufacturing, where tiny, intricate components must be produced with extreme accuracy.
Drills are used to create holes, while saws cut through materials, and milling cutters shape and finish surfaces. These tools are made from durable materials like carbide and high-speed steel to withstand the rigors of cutting through tough materials. Proper use and maintenance of cutting tools are crucial to ensure their longevity and the quality of the parts produced.
Cutting tools play a crucial role in achieving precision and consistency, making them indispensable in many industries. Their ability to produce detailed and accurate components is key to maintaining high standards and meeting specific manufacturing requirements.
Injection Molds
Injection molds are critical in plastic manufacturing, allowing for the mass production of parts with consistent quality. These molds shape molten plastic into specific forms, ranging from simple items like toys to complex medical devices. The injection molding process involves injecting molten plastic into a mold cavity, where it cools and solidifies into the desired shape.
Injection molds are highly efficient and cost-effective, making them ideal for large-scale production. They are made from durable materials like steel or aluminum to withstand repeated use. The precision of injection molds ensures that each part produced is identical, maintaining high quality and reducing waste.
In various industries, from consumer goods to healthcare, injection molds enable the creation of complex plastic parts with high precision and consistency. Investing in high-quality molds and proper maintenance ensures long-term reliability and cost savings in the production process.
CNC Machines
Computer Numerical Control (CNC) machines are automated tools that use computer programs to control their movements. These machines can perform various tasks with high precision, including:
- Cutting
- Drilling
- Milling
CNC machines are used in industries like aerospace, automotive, and electronics, where intricate and detailed parts are required.
CNC machines offer unparalleled accuracy and repeatability. They can produce complex shapes and designs that would be difficult or impossible with manual tools. The automation provided by CNC machines also increases efficiency and reduces the likelihood of human error, leading to consistent, high-quality results.
Extrusion Tools
Extrusion tools create objects with a fixed cross-sectional profile by pushing material through a die. This process is commonly used for making long shapes like pipes, tubes, and sheets from metals or plastics. Extrusion tools are essential in construction and manufacturing industries due to their ability to produce uniform parts in large quantities.
Extrusion allows for continuous production, making it a cost-effective method for manufacturing products with consistent cross-sections. The versatility of extrusion tools enables the creation of complex profiles and the use of various materials, enhancing their application across different industries.
Grinding Tools
Grinding tools remove excess material and smooth surfaces, essential for achieving a high-quality finish on metal and plastic parts. These tools are commonly used in the automotive and aerospace industries to ensure components meet precise specifications and perform reliably.
Grinding tools include various types of grinders, such as surface, cylindrical, and centerless grinders. They are designed to handle different materials and shapes, providing flexibility and precision in the finishing process. Proper use and maintenance of grinding tools are crucial to achieving the desired surface quality and extending tool life.
Welding Tools
Welding tools join metal parts by melting the edges and applying pressure. These tools are critical in industries requiring strong, durable joints, such as:
- Construction
- Automotive
- Shipbuilding
Various welding techniques, including MIG, TIG, and spot welding, are used depending on the materials and requirements.
Welding tools must be precise and reliable to ensure strong, high-quality welds. Proper training and maintenance are essential to maximize the effectiveness of welding tools and ensure the safety of the operators. Welding plays a vital role in manufacturing robust structures and components.
Laser Cutting Tools
Laser cutting tools use a focused laser beam to cut materials with high precision. These tools can cut complex shapes and fine details, making them ideal for industries like:
- Electronics
- Jewelry
- Custom manufacturing
Laser cutting is a non-contact process, reducing the risk of material deformation and ensuring a clean finish.
Laser-cutting tools offer flexibility in material choice, including metals, plastics, and ceramics. They provide high accuracy and efficiency, allowing for the rapid production of detailed parts. The use of laser-cutting tools can significantly enhance the quality and speed of the manufacturing process.
Measuring Tools
Measuring tools ensure parts meet precise specifications, critical for maintaining quality and consistency in manufacturing. These tools include calipers, micrometers, and coordinate measuring machines (CMMs). Accurate measurement is essential in industries like:
- Aerospace
- Automotive
- Electronics
These are industries where precision is paramount.
Measuring tools help detect deviations and ensure that each part produced adheres to the required standards. Regular calibration and maintenance of measuring tools are necessary to maintain their accuracy. Using high-quality measuring tools can prevent costly errors and rework, enhancing overall production efficiency.
Surface Finishing Tools
Surface finishing tools enhance the appearance and performance of manufactured parts. Techniques such as polishing, plating, and coating improve the surface quality and durability of components. These tools are essential in industries where aesthetics and functionality are equally important, such as consumer electronics and automotive.
Surface finishing tools provide the final touch to products, ensuring they meet both visual and performance standards. Proper surface finishing can improve resistance to wear, corrosion, and other environmental factors. Investing in quality surface finishing tools can significantly enhance the overall quality and longevity of the products.
Maintenance of OEM Tools
Proper maintenance of OEM tools is vital for ensuring their longevity and performance. Regular inspections, cleaning, and calibration help prevent breakdowns and maintain consistent results.
By dedicating time to maintenance, manufacturers can reduce downtime and extend the life of their tools. Well-maintained tools contribute to higher production efficiency and better-quality products, leading to long-term savings and reliability.
OEM Trends to Watch Out For
The future of OEM tools looks promising with advances in technology like 3D printing and artificial intelligence. These innovations open new possibilities for precision, efficiency, and customization in manufacturing.
Staying informed about emerging trends and integrating new technologies can help manufacturers remain competitive. Embracing future developments in OEM tools will lead to improved processes and higher-quality products.
Embracing OEM Tools
Embracing OEM tools can transform your manufacturing process. The right tools allow you to produce higher-quality products more efficiently. OEM tools are crucial in industries such as automotive, aerospace, and consumer goods.
Ready to take your manufacturing to the next level? Contact Shield Works for customized OEM manufacturing, assembly, and warehousing solutions within secure, IPR-protective production zones. Benefit from 16 years of China-based experience and enjoy risk-free, internationally recognized quality standards.
From Concept to Consumer: The Journey of Industrial Design in China

Industrial design is the marriage of creativity and functionality. It’s about taking a simple idea and transforming it into a tangible product that not only works well but looks great too. In China, a global leader in manufacturing, industrial design plays a crucial role in bringing innovative concepts to life for consumers worldwide. This blog post will unveil the intriguing journey of industrial design in China, following a product from its initial spark of an idea to its final destination on store shelves.
What Is the Industrial Design
Industrial design is a discipline that marries functionality with aesthetics to develop the products that populate our everyday lives. This field is inherently multidisciplinary, drawing on areas such as product design, engineering, and user experience to ensure that every item is not just pleasing to the eye, but also serves its intended purpose effectively. It involves a deep understanding of both the material and the immaterial aspects of a product—its form, usability, and how it fits within the broader context of human needs and environments.
At its heart, industrial design focuses on solving problems through design; it is about creating solutions that enhance the user experience in innovative ways. This could range from designing a more comfortable chair to developing a smartphone with a user-friendly interface. The essence of industrial design lies in its ability to transform an idea into a tangible entity that combines utility with beauty, making our interactions with products smoother and more enjoyable. Through a process that includes research, conceptualization, refinement, and testing, industrial designers strive to bring new products and experiences to life, shaping the way we live, work, and play.
What Is the Goal of Industrial Product Design
The primary objective of industrial product design is to merge form with function in a way that not only solves practical problems but also elicits an emotional response from the user. It’s about creating products that people not only need but desire. This involves a careful balancing act between aesthetics, usability, cost-efficiency, and sustainability. Designers must consider the lifecycle of a product, from the materials used in its construction to its end-of-life disposal or recycling, ensuring it meets the requirements of consumers, manufacturers, and the environment.
Another essential goal is to enhance the user experience, making products more intuitive, accessible, and enjoyable to use. This user-centered approach helps in identifying and innovating on aspects of products that can significantly improve daily life. In doing so, industrial product design contributes to building a brand’s identity and competitive edge in the market, fostering loyalty and trust among users. Through the lens of industrial design, products become more than just objects; they transform into experiences that connect with users on a deeper level, ultimately shaping the fabric of society by enhancing the quality of life and fostering sustainable practices.
What is the Process of Industrial Design
The process of industrial design is intricate, blending art with engineering to craft products that are as functional as they are visually appealing.
1. Ideation and Conceptualization
The first step in the industrial design process is ideation and conceptualization. This phase involves generating ideas and concepts that address a specific problem or fulfill a market need. Designers often begin with brainstorming sessions, sketching out rough ideas, and exploring various possibilities. They consider user needs, market trends, and technological advancements. This stage is highly creative and requires thinking outside the box to propose innovative solutions. The goal is to come up with a broad range of ideas that can later be refined and developed further.
2. Design and Development
Once a promising idea has been identified, the design and development phase begins. This stage involves transforming the initial concept into a more detailed and workable design. Designers create detailed sketches, 3D models, and technical drawings using software tools. They consider factors such as aesthetics, functionality, ergonomics, and usability. Collaboration with other professionals, such as engineers and marketing experts, is crucial to ensure that the design meets all requirements and constraints. This phase also involves iterative refinement, where the design is continuously improved based on feedback and testing.
3. Prototyping
Prototyping is a critical step in the industrial design process where a tangible model of the product is created. This can be done using various methods such as 3D printing, CNC machining, or handmade models. Prototypes help designers and stakeholders visualize the product and assess its form, fit, and function. It allows for hands-on testing and identification of potential issues that were not apparent in the digital models. Prototyping is an iterative process, often involving multiple versions before a satisfactory model is achieved.
4. Testing and Evaluation
After creating prototypes, the next phase is testing and evaluation. This involves rigorous testing of the prototype to ensure it meets all design specifications and user requirements. Testing can include usability studies, performance tests, and safety evaluations. Feedback from these tests is used to make necessary adjustments and improvements to the design. Evaluation also considers factors such as cost, production feasibility, and market viability. This step is crucial to ensure that the product not only performs well but also meets regulatory standards and consumer expectations.
5. Engineering and Detailing
With a validated design, the process moves into engineering and detailing. This stage involves developing the final technical specifications and detailed drawings required for manufacturing. Engineers work on aspects such as material selection, structural integrity, and assembly processes. Detailed CAD models and technical drawings are produced to guide the manufacturing process. This phase ensures that the design is practical and can be produced efficiently and cost-effectively. It also involves finalizing details such as surface finishes, color schemes, and branding elements.
6. Manufacturing
The final step in the industrial design process is manufacturing. This phase involves setting up production lines, sourcing materials, and starting the mass production of the product. Close collaboration with manufacturers is essential to ensure that the product is made to the required specifications and quality standards. During this phase, any final adjustments or optimizations to the production process are made. Quality control measures are implemented to maintain consistency and ensure that each unit meets the desired standards. Once manufacturing is complete, the product is ready for distribution and market launch.
If you’re seeking an industry design company to support your business, look no further than Shield Works. We offer comprehensive OEM manufacturing, assembly, and warehousing solutions tailored to meet your needs. Our transparent, open, and flexible working practices ensure a seamless collaboration. As a 100% Western-owned company, we have a deep understanding of your goals. Discover the benefits we provide by speaking with a representative today.
Five Critical Mistakes in Product Development and How to Avoid Them

The journey from a product idea to a successful launch can be exciting, but it’s also fraught with potential hazards. Many great ideas stumble along the way due to avoidable mistakes. To increase the chances of success for your product, it’s important to understand and avoid common mistakes in product development. By recognizing these common pitfalls, you can significantly increase your chances of bringing a winning product to the market. In this blog, we’ll explore five frequent product development mistakes and how to steer clear of them.
1. Skipping Market Research
One of the most significant and costly mistakes in product development is neglecting proper market research. Understanding your target audience, their needs, preferences, and the existing competition is crucial.
Why It’s a Mistake
The consequences of skipping this step are multifold. Without a solid grasp on what potential customers are looking for, there’s a significant risk of creating a product that doesn’t fulfill any actual needs or desires, rendering it irrelevant upon launch. Similarly, ignorance of competitors’ strengths and weaknesses can result in a product that is indistinguishable from others, lacking a unique value proposition to stand out in a crowded marketplace.
How To Avoid It
Invest in qualitative and quantitative research to gather insights about your potential customers. Conduct surveys, focus groups, and interviews to test your assumptions. Additionally, analyze your competitors to understand what works, what doesn’t, and how you can differentiate your product.
2. Overlooking Product Validation
A grave oversight in the journey of product development is the neglect of product validation. This stage is crucial for verifying that your idea has real demand in the market and meets the expectations of your target audience.
Why It’s a Mistake
Product validation should be viewed as an essential mechanism for risk management, allowing developers to identify and address potential issues before they become costly errors. Employing strategies such as developing prototypes, conducting focus groups, and initiating beta testing provides a platform for gathering actionable feedback. This feedback serves as a guide to refine your product, ensuring it aligns with customer needs and preferences.
How To Avoid It
Integrating thorough product validation early and throughout the development process is indispensable. Focus on user experience (UX) from the earliest stages of development. Incorporate user feedback through prototype testing and make adjustments based on real user interactions. Prioritize simplicity and ensure that your product can be used easily by your target demographic. These approaches enable you to build a product not on assumptions but on verified customer desires and feedback, setting a solid foundation for its launch and acceptance in the competitive market landscape.
3. Ignoring Feedback and Iteration
Many product developers make the mistake of sticking too rigidly to their initial vision without allowing room for iteration based on feedback. This can result in a product that does not fully resonate with its intended market.
Why It’s a Mistake
Ignoring constructive feedback and iteration can act as a significant roadblock, hindering your ability to uncover flaws and identify potential enhancements that could substantially elevate both the appeal and functionality of your product. When you dismiss valuable insights and suggestions from users, you run the risk of stagnation or even regression in your product’s development.
How To Avoid It
Actively seeking out and integrating feedback is a strategic approach that facilitates product growth and innovation. It enables developers and product managers to make informed adjustments that can significantly elevate a product’s market fit and user satisfaction. This could involve tweaking features, resolving user experience issues, or adding new functionalities that address emerging needs.
4. Mismanaging Development Costs
Cost overruns are exceedingly common in product development projects. Without careful budget management, your project can become financially unfeasible.
Why It’s a Mistake
Without diligent budget oversight and cost management, projects can quickly overrun their allocated budgets, leading to difficult decisions that may compromise the quality or scope of the product. Effective cost management requires a detailed budget that accounts for all potential expenditures, including materials, labor, technology, and unforeseen expenses.
How To Avoid It
Regular monitoring and review of expenses against this budget are essential to identify and address overruns as they occur. Additionally, plan your budget meticulously and monitor spending closely. Always include a contingency fund for unexpected expenses. Make strategic decisions about where to allocate resources to maximize the impact on product quality and customer satisfaction.
5. Compromising on Quality for Speed
Shortcuts in development may accelerate timelines, but they frequently lead to a product that falls short of both company standards and customer expectations.
Why It’s a Mistake
High-quality products are the foundation of customer trust and product longevity. When quality is compromised to expedite development, the result can be an increase in customer dissatisfaction, negative reviews, and a damaging impact on brand reputation. Such outcomes not only undermine the immediate product launch but can also have ripple effects on future products and the overall perception of the brand.
How To Avoid It
Investing the necessary time to thoroughly test and refine a product pays dividends in the form of reliability, user satisfaction, and competitive advantage. It’s essential to integrate quality assurance processes throughout the development cycle, ensuring that every feature and function meets the highest standards. This includes rigorous testing phases, which, while time-consuming, are indispensable for identifying and rectifying potential issues before they reach the end user.
Optimizing Your Product Development Process
Effective product development is all about creating a product that meets a need in the market and doing so in a way that’s efficient and avoids wasting time and resources. Avoiding these common mistakes in product development can markedly increase your chances of success.
Should you have any queries or require additional assistance with your product development strategy, feel free to contact our team at Shield Works. Partnering with us not only refines your strategy but also enhances your chances of achieving your goals. Together, we can turn your innovative ideas into successful products.
A Guide to Electronic Contract Manufacturing Services

As you scale your business, you need to make sure you can keep up with production demands. How can you efficiently manage manufacturing electric parts while focusing on growing your business?
The answer is to utilize electronic contract manufacturing services. By outsourcing your manufacturing needs, you can access specialized expertise, advanced technology, and cost savings.
Join us as we delve into the benefits of electronic contract manufacturing services, key components to look for, how to choose the right partner, and more!
Understanding Electronic Contract Manufacturing Services
Electronic contract manufacturing services involve outsourcing the production of electronic parts to specialized companies. These services cover various stages of manufacturing, from design and development to production and assembly.
Businesses use these services to leverage the expertise and advanced technology of manufacturing companies. This allows businesses to produce high-quality electronic parts without investing in expensive equipment or facilities.
By outsourcing, companies can focus on their core activities while the manufacturing company handles the production process. This approach helps businesses reduce costs, improve efficiency, and stay competitive in the market.
Benefits of Manufacturing Outsourcing
One of the most significant advantages is cost savings. By outsourcing, companies can reduce overhead and operational costs.
They don’t need to invest in expensive equipment or facilities. This allows them to allocate resources more efficiently. Another benefit is access to advanced technology and expertise.
Manufacturing companies often have specialized skills and equipment that businesses might not possess. This ensures high-quality production and innovation.
Flexibility in production capacity is another key advantage. Businesses can scale their production up or down based on demand without the constraints of fixed resources.
This adaptability helps companies respond quickly to market changes. Outsourcing manufacturing also allows businesses to focus on their core activities. Instead of managing production, they can concentrate on research, marketing, and customer service. This focus can drive growth and enhance competitiveness.
Plus, manufacturing companies often have robust supply chain management systems. They can source materials efficiently and manage logistics, ensuring timely delivery of products. This reduces the risk of delays and disruptions in the production process.
Key Components
Electronic contract manufacturing involves several key components that ensure the production of high-quality electronic parts. One of the first steps is design and development.
Manufacturing companies often assist in designing products to meet specific requirements and standards. This step ensures that the final product is both functional and reliable. Prototyping and testing follow the design phase.
Prototypes are created to test the product’s functionality and performance. Testing helps identify any issues that need to be addressed before full-scale production begins.
The next component is production and assembly. This involves the actual manufacturing process where electronic parts are produced in large quantities. Manufacturing companies use advanced machinery and technology to ensure precision and efficiency in production.
Assembly is a critical step where various components are put together to form the final product. This process requires skilled workers and strict quality control measures to ensure everything fits and works correctly.
Supply chain management is another important aspect. Manufacturing companies handle sourcing materials and managing logistics to ensure a smooth production process.
They have established relationships with suppliers, which helps in obtaining high-quality materials at competitive prices. Effective supply chain management also ensures timely delivery of materials and products, reducing the risk of production delays.
Choosing the Right Manufacturing Company
First, consider the company’s certifications and quality standards. A reliable manufacturing company should adhere to industry standards, ensuring that their processes and products meet high-quality benchmarks. This is important to maintain the integrity and reliability of your products.
Experience and expertise are important too. Look for a company with a proven track record in electronic parts manufacturing.
An experienced company will have the knowledge and skills necessary to handle complex production processes. They’ll also be better equipped to deal with any challenges that may arise during manufacturing.
Production capacity is another key consideration. Ensure that the manufacturing company can meet your production needs. This includes being able to scale up production if demand increases.
It’s important to choose a company that has the technological capabilities to handle your specific requirements. Advanced machinery and technology are vital for precision and efficiency in production.
Finally, take a look at the company’s reputation. Look for reviews and testimonials from other businesses that have used their services. A good reputation often indicates a reliable and trustworthy manufacturing partner.
Potential Challenges and Solutions
One common issue is communication. Working with a manufacturing company often involves coordinating across different locations and time zones. Misunderstandings can occur, leading to production delays or errors.
To avoid this, it’s important to establish clear communication channels and protocols. Regular updates and meetings can help ensure everyone is on the same page.
Quality control is another concern. When you outsource production, you rely on another company to maintain the quality of your products. This can be risky if the manufacturing partner does not meet your standards.
To address this, set strict quality requirements from the beginning. Regular inspections and audits can help ensure the manufacturing company adheres to these standards.
Intellectual property protection is also a critical issue. Sharing designs and processes with an external company can expose your business to risks of theft or misuse.
Protecting your intellectual property involves having strong legal agreements in place. Non-disclosure agreements and other legal measures can help safeguard your proprietary information.
Establishing clear contracts and agreements is essential to avoid misunderstandings and ensure smooth operations. Detailed contracts should outline all aspects of the partnership, including production schedules, quality standards, and payment terms.
Smart Moves to Grow Your Business
Electronic contract manufacturing services offer businesses a path to efficiency, cost savings, and growth. By outsourcing production, companies can focus on core activities, ensuring high-quality electronic parts while staying competitive in the market. Embrace these services to drive your business forward.
Shield Works is a WFOE (Wholly Foreign Owned Enterprise) setup in full accordance with PRC laws and regulations for assembly, manufacturing, and product distribution and exportation.
We believe in Western standards of service, communications, and quality. Contact us today for your needs in product assembly, warehousing and distribution services in China, and more!