Posts Tagged ‘Customised Manufacturing’
A Beginner’s Guide to OEM Tools
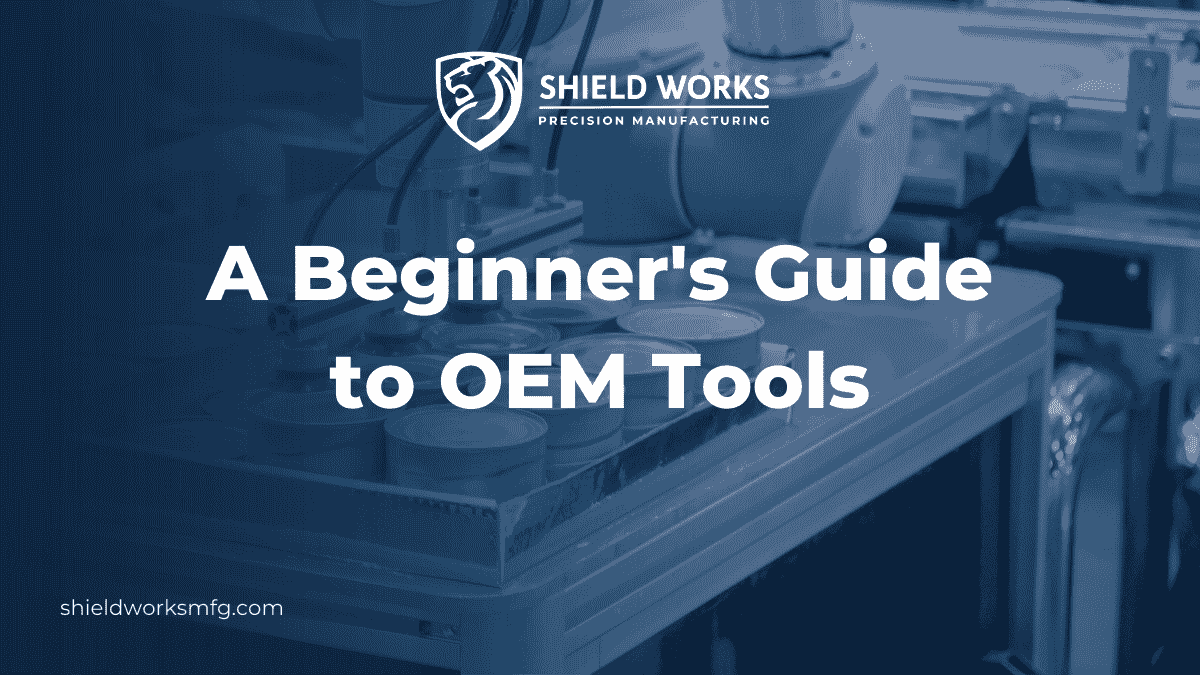
Have you wondered what drives the production of your favorite gadgets and vehicles? OEM tools have revolutionized the way we manufacture products, creating endless possibilities for innovation and efficiency.
These tools are the unsung heroes behind many of the high-quality products we use daily. Understanding these tools is key to staying ahead in the fast-paced world of manufacturing.
Imagine producing components that fit perfectly and function smoothly every time. That’s the power of OEM tools. They help create better products, leading to happier customers and fewer returns.
In this guide, we’ll dive into the exciting world of OEM tools and explore what you need to know to get started. Whether you’re new to manufacturing or looking to update your knowledge, this guide is your starting point. Let’s unlock the secrets of OEM tools together.
What Are OEM Tools?
OEM stands for Original Equipment Manufacturer. OEM tools are used in the production of parts and equipment that will be sold under another company’s brand. These tools are essential for creating high-quality, reliable products. They ensure that every component fits perfectly and functions smoothly.
Without OEM tools, the production process would be slower, less precise, and more prone to errors. This would lead to increased costs and lower-quality products.
OEM tools come in various forms, each designed for specific tasks. Some common types include:
- Stamping tools
- Cutting tools
- Injection molds
Stamping tools are used to cut or shape metal parts while cutting tools remove material to create the desired shape. Injection molds, on the other hand, are used in plastic manufacturing to produce parts with consistent quality.
These tools are critical in many industries, including:
- Automotive
- Aerospace
- Electronics
- Consumer goods
In the automotive industry, for example, stamping tools are used to create complex metal parts that must meet strict safety standards. In electronics, precision cutting tools are needed to manufacture small, intricate components.
Using OEM tools also helps manufacturers maintain high standards and produce goods that meet specific requirements. This results in better products and greater customer satisfaction. Furthermore, OEM tools allow for mass production without compromising quality, making it possible to meet the demands of a growing market.
Understanding OEM tools is essential for anyone involved in manufacturing. By using these tools effectively, manufacturers can improve their production processes, reduce costs, and deliver high-quality products that meet or exceed customer expectations.
Why OEM Tools Matter
OEM tools play a crucial role in product manufacturing. They ensure that every component fits perfectly and functions smoothly.
High-quality OEM tools lead to better products, which means happier customers and fewer returns. This is because OEM tools allow for precision and consistency in the manufacturing process.
The use of OEM tools helps reduce production time and costs, making manufacturing more efficient.
By speeding up the production process and minimizing errors, these tools help manufacturers save money and increase output. This efficiency is vital in competitive industries where time and cost savings can make a significant difference.
With the right OEM tools, manufacturers can achieve the precision needed for complex and detailed parts. This is especially important in industries like automotive, aerospace, and electronics, where even small deviations can lead to significant issues.
For example, in the automotive industry, the precise fitting of parts can affect the safety and performance of vehicles. In electronics, tiny components must fit perfectly to ensure the proper functioning of devices.
OEM tools also contribute to product innovation. As technology advances, the need for new and improved tools grows. This drives the development of cutting-edge OEM tools that can handle new materials and manufacturing techniques.
By staying up-to-date with the latest OEM tools, manufacturers can remain competitive and continue to meet the evolving demands of the market.
OEM Tool Options in Detail
OEM tools are diverse and specialized, each designed for specific tasks in various types of manufacturing processes. Understanding the various types of OEM tools can help manufacturers choose the right tools for their needs, ensuring precision, efficiency, and high-quality output.
In this section, we will explore the different types of OEM tools in detail, discussing their:
- Functions
- Applications
- Benefits
From stamping and cutting tools to injection molds and more advanced equipment, we will cover a broad range of tools essential for various manufacturing processes. So here they are in more detail:
Stamping Tools
Stamping tools are essential in industries requiring high precision and durability, such as automotive and aerospace. These tools cut, shape, or emboss metal sheets into desired forms using a process called stamping. The metal sheet is placed into a stamping press, where a tool and die surface form the metal into a new shape.
There are various types of stamping tools, including dies, presses, and punches. Dies cut or shape material, while presses exert high pressure to form the metal. Single-station dies perform one operation, and progressive dies perform multiple operations in a single cycle.
Stamping tools can produce complex shapes quickly and accurately, crucial for automotive parts like body panels and chassis components. In the aerospace sector, stamping tools create parts that require exceptional strength and precision, using metals like aluminum, steel, and titanium.
Overall, stamping tools provide high precision, durability, and efficiency. By investing in quality tools and proper maintenance, manufacturers can achieve consistent, high-quality results.
Cutting Tools
Cutting tools are vital in manufacturing, designed to remove material from a workpiece to create the desired shape and size. These tools come in various forms, including:
- Drills
- Saws
- Milling cutters
They are essential for processes that require high precision and fine detail, such as electronics manufacturing, where tiny, intricate components must be produced with extreme accuracy.
Drills are used to create holes, while saws cut through materials, and milling cutters shape and finish surfaces. These tools are made from durable materials like carbide and high-speed steel to withstand the rigors of cutting through tough materials. Proper use and maintenance of cutting tools are crucial to ensure their longevity and the quality of the parts produced.
Cutting tools play a crucial role in achieving precision and consistency, making them indispensable in many industries. Their ability to produce detailed and accurate components is key to maintaining high standards and meeting specific manufacturing requirements.
Injection Molds
Injection molds are critical in plastic manufacturing, allowing for the mass production of parts with consistent quality. These molds shape molten plastic into specific forms, ranging from simple items like toys to complex medical devices. The injection molding process involves injecting molten plastic into a mold cavity, where it cools and solidifies into the desired shape.
Injection molds are highly efficient and cost-effective, making them ideal for large-scale production. They are made from durable materials like steel or aluminum to withstand repeated use. The precision of injection molds ensures that each part produced is identical, maintaining high quality and reducing waste.
In various industries, from consumer goods to healthcare, injection molds enable the creation of complex plastic parts with high precision and consistency. Investing in high-quality molds and proper maintenance ensures long-term reliability and cost savings in the production process.
CNC Machines
Computer Numerical Control (CNC) machines are automated tools that use computer programs to control their movements. These machines can perform various tasks with high precision, including:
- Cutting
- Drilling
- Milling
CNC machines are used in industries like aerospace, automotive, and electronics, where intricate and detailed parts are required.
CNC machines offer unparalleled accuracy and repeatability. They can produce complex shapes and designs that would be difficult or impossible with manual tools. The automation provided by CNC machines also increases efficiency and reduces the likelihood of human error, leading to consistent, high-quality results.
Extrusion Tools
Extrusion tools create objects with a fixed cross-sectional profile by pushing material through a die. This process is commonly used for making long shapes like pipes, tubes, and sheets from metals or plastics. Extrusion tools are essential in construction and manufacturing industries due to their ability to produce uniform parts in large quantities.
Extrusion allows for continuous production, making it a cost-effective method for manufacturing products with consistent cross-sections. The versatility of extrusion tools enables the creation of complex profiles and the use of various materials, enhancing their application across different industries.
Grinding Tools
Grinding tools remove excess material and smooth surfaces, essential for achieving a high-quality finish on metal and plastic parts. These tools are commonly used in the automotive and aerospace industries to ensure components meet precise specifications and perform reliably.
Grinding tools include various types of grinders, such as surface, cylindrical, and centerless grinders. They are designed to handle different materials and shapes, providing flexibility and precision in the finishing process. Proper use and maintenance of grinding tools are crucial to achieving the desired surface quality and extending tool life.
Welding Tools
Welding tools join metal parts by melting the edges and applying pressure. These tools are critical in industries requiring strong, durable joints, such as:
- Construction
- Automotive
- Shipbuilding
Various welding techniques, including MIG, TIG, and spot welding, are used depending on the materials and requirements.
Welding tools must be precise and reliable to ensure strong, high-quality welds. Proper training and maintenance are essential to maximize the effectiveness of welding tools and ensure the safety of the operators. Welding plays a vital role in manufacturing robust structures and components.
Laser Cutting Tools
Laser cutting tools use a focused laser beam to cut materials with high precision. These tools can cut complex shapes and fine details, making them ideal for industries like:
- Electronics
- Jewelry
- Custom manufacturing
Laser cutting is a non-contact process, reducing the risk of material deformation and ensuring a clean finish.
Laser-cutting tools offer flexibility in material choice, including metals, plastics, and ceramics. They provide high accuracy and efficiency, allowing for the rapid production of detailed parts. The use of laser-cutting tools can significantly enhance the quality and speed of the manufacturing process.
Measuring Tools
Measuring tools ensure parts meet precise specifications, critical for maintaining quality and consistency in manufacturing. These tools include calipers, micrometers, and coordinate measuring machines (CMMs). Accurate measurement is essential in industries like:
- Aerospace
- Automotive
- Electronics
These are industries where precision is paramount.
Measuring tools help detect deviations and ensure that each part produced adheres to the required standards. Regular calibration and maintenance of measuring tools are necessary to maintain their accuracy. Using high-quality measuring tools can prevent costly errors and rework, enhancing overall production efficiency.
Surface Finishing Tools
Surface finishing tools enhance the appearance and performance of manufactured parts. Techniques such as polishing, plating, and coating improve the surface quality and durability of components. These tools are essential in industries where aesthetics and functionality are equally important, such as consumer electronics and automotive.
Surface finishing tools provide the final touch to products, ensuring they meet both visual and performance standards. Proper surface finishing can improve resistance to wear, corrosion, and other environmental factors. Investing in quality surface finishing tools can significantly enhance the overall quality and longevity of the products.
Maintenance of OEM Tools
Proper maintenance of OEM tools is vital for ensuring their longevity and performance. Regular inspections, cleaning, and calibration help prevent breakdowns and maintain consistent results.
By dedicating time to maintenance, manufacturers can reduce downtime and extend the life of their tools. Well-maintained tools contribute to higher production efficiency and better-quality products, leading to long-term savings and reliability.
OEM Trends to Watch Out For
The future of OEM tools looks promising with advances in technology like 3D printing and artificial intelligence. These innovations open new possibilities for precision, efficiency, and customization in manufacturing.
Staying informed about emerging trends and integrating new technologies can help manufacturers remain competitive. Embracing future developments in OEM tools will lead to improved processes and higher-quality products.
Embracing OEM Tools
Embracing OEM tools can transform your manufacturing process. The right tools allow you to produce higher-quality products more efficiently. OEM tools are crucial in industries such as automotive, aerospace, and consumer goods.
Ready to take your manufacturing to the next level? Contact Shield Works for customized OEM manufacturing, assembly, and warehousing solutions within secure, IPR-protective production zones. Benefit from 16 years of China-based experience and enjoy risk-free, internationally recognized quality standards.
What Is a Contract Manufacturer?

Imagine running a business that operates so smoothly that you never have to worry about interruptions. You have no issue maintaining productivity, boosting employee morale, and meeting customer needs. This is the reality for those who work with the right manufacturing services.
Many companies choose to hire contract manufacturers. Not everyone understands how they function, though. So, what is a contract manufacturer?
We’ve created a brief guide with the key information you need to know so you can make the right decision. Listed below are some of the most notable.
What Is a Contract Manufacturer?
As the name implies, a contract manufacturer is a firm that offers manufacturing services on a contract basis. These are great for those who don’t have access to their own manufacturing facility.
Contract manufacturers come in various forms, and each specializes in different services. Each type of manufacturer has its own set of specialized equipment, workflow, and knowledge.
This allows them to efficiently produce their products. Electronics manufacturers might offer services like circuit board assembly and electronic device manufacturing.
Pharmaceutical contract manufacturers focus on drug formulation, compliance standards, and secure packaging. Understanding the different types of manufacturers will help you find the best one for your situation. Keep this in mind when moving forward.
Types of Manufacturing Services
Contract manufacturers offer no shortage of services during the manufacturing process. Having access to these will help you fill in gaps and get comprehensive results. Let’s explore them below.
Design Assistance
This service involves helping clients with technical drawings, material sourcing, and production methods. The stronger your design, the more integrity your products will have.
Contract manufacturers are great resources for businesses with complex designs. Working with these without assistance can be stressful and lead to further complications.
Prototyping
Prototypes are essential for assessing your design before mass production. If your product doesn’t function correctly, you can make the required changes before investing in production. Your manufacturer can also come up with multiple different prototypes and then determine which is best.
Product Manufacturing
This can include the sourcing of materials, fabrication, and assembly. This is one of the most common ways manufacturing companies help businesses.
Their level of involvement will depend on your needs. Some companies need full-service manufacturing, while others only need assistance with minor obligations.
Quality Control
This process ensures that your products meet quality standards and function as expected. QC standards go a long way toward preserving your brand’s reputation, as well. They’ll also help you develop a comprehensive quality control process.
Packaging and Shipping
Preparing products for shipment is often arduous work. The same can be said about handling logistics. Managing these with a professional will prevent you from making costly mistakes and reduce the time you spend.
Benefits of Contract Manufacturing
Utilizing a contract manufacturer comes with no shortage of benefits. Leveraging these can help you bring your vision to life. Let’s look closer at some of the key advantages.
Cost Efficiency
Working with contract manufacturers offers reduced overhead costs. There’s no need to maintain manufacturing facilities or purchase expensive equipment. You can then invest the money you save in other areas of your business.
Scalability
You’ll have no issue adjusting your production levels to scale with your company. For instance, you might need to ramp up manufacturing during peak seasons. Slower months may not require as many resources.
Focus on Core Responsibilities
When you delegate manufacturing services to another company, you can focus on core obligations. This will alleviate substantial stress and make it easier to reach your goals. Small businesses can benefit substantially, as they often don’t have abundant time and resources.
Access to Expertise
Contract manufacturers have advanced skills and knowledge of contemporary technology. You can utilize these attributes to expand your own knowledge, as well. A common way to do so is through gaining insight into areas of concern you can improve.
Speed to Market
Faster production times help products reach the market quicker. This minimizes delays and helps keep your customers satisfied.
This attribute will also make it easier to fulfill pre-orders for products. There’s nothing worse for your reputation than falling short of your promises.
Choosing the Right Contract Manufacturer
Not all manufacturers are created equal, and it’s imperative to make the right choice before moving forward. This will help ensure you make the best choice for your needs.
You can start by researching their past reputation online. See what other people have to say about the results they got. Were they satisfied with their experience?
Did they encounter issues the provider couldn’t help them overcome? The answers to questions like these will help ensure you make the right choice.
What is their pricing structure like? You tend to get what you pay for, and it’s never recommended to choose the cheapest options. There’s a point of diminishing returns regarding what you spend, though.
Paying top prices for manufacturing services won’t always guarantee better results. Instead, look for someone in the middle of the industry’s price range.
This will help you meet your goals without stretching your budget. They should have plenty of experience working with companies like yours.
Growing your business is only possible when they understand your project’s nuances. Ideally, you’ll find someone with at least a decade’s worth of experience.
Settling for less is never recommended. As long as you stay vigilant during your search, you shouldn’t encounter issues finding the best option for your needs.
Take Action as Soon as Possible
The longer you wait to employ contract manufacturing services, the more difficult it will be to reach your goals. The answer to “What is a contract manufacturer” will help you make the right choice. Just be sure to research the provider you work with.
Shield Works offers customized OEM manufacturing, assembly, and warehousing solutions. We have over 19 years of experience in China-based manufacturing, allowing us to exceed all expectations.
We also provide transparency throughout the process to offer key insights. You’ll learn more about how we can help when you get in touch with a representative today.
6 Key Considerations Before Mass Producing Your Designed Product

Congratulations! You’ve poured your heart and soul into designing a fantastic product. Now, the excitement builds as you envision it lining store shelves or filling online orders. But hold on a minute – before diving headfirst into mass production, there are key considerations to ensure your brilliant creation translates seamlessly from prototype to reality.
In this blog, we’ll explore 7 crucial factors to think about before mass producing your designed product. By addressing these aspects upfront, you can streamline the process, minimize hiccups, and ultimately launch a product that exceeds expectations.
1. Review Design Thoroughly
This might seem obvious, but it’s crucial. Before mass production begins, double-checking your product design is imperative. This proactive approach not only minimizes the risk of product recalls or failures but also helps maintain your brand’s reputation by ensuring customer satisfaction.
The product should not only function well but also appeal to consumers. This means paying close attention to the ergonomics and aesthetics of the design. Ensure that the product is user-friendly and that its physical layout accommodates usability. Aesthetically, the product should align with current market trends and the expectations of your target audience.
In addition, work closely with your manufacturing team to ensure that the design is optimized for production. This often involves simplifying the design to reduce manufacturing complexity and costs while maintaining product integrity.
2. Assess Manufacturing Capability
Not all manufacturers are created equal. Choosing the right partner is critical for the quality and cost-effectiveness of your mass production. Imagine this: your design is intricately detailed, requiring specialized machinery and components. To gauge your manufacturer’s capabilities effectively, consider asking the following questions:
- What machinery and technology are available?
- Does the facility have the capability to scale operations up or down based on demand?
- What volume of products can be manufactured within a given time frame?
To ensure all aspects are covered, prepare a detailed checklist that includes equipment specifications, material sourcing, quality control measures, and timelines. This proactive approach facilitates a clear dialogue between you and the manufacturer, setting the foundation for a robust partnership and a successful product launch.
3. Conduct Cost Analysis
Mass production is an investment. Before diving in, conduct a thorough cost analysis to understand the financial implications. Consider these factors:
- Material Costs: Get quotes for the materials needed to produce your product in bulk. This might involve negotiations with potential suppliers to secure the best price for your order volume.
- Manufacturing Costs: Obtain quotes from potential manufacturers. These quotes should account for labor costs, overhead, and any potential tooling or setup fees.
- Shipping & Logistics: Factor in the costs of shipping your finished product from the manufacturer to your warehouse or distribution center.
- Packaging Costs: Don’t underestimate the cost of packaging! Explore different options to find a balance between functionality, aesthetics, and cost.
Remember, don’t settle for the first quote. Obtain estimates from several manufacturers to find the best balance between cost, quality, and production speed.
4. Select and Source Materials
Choosing the right materials for your product is not only a matter of quality but also sustainability and cost-efficiency. It’s essential to conduct a thorough investigation into the types of materials that will best serve the purpose of your product while aligning with your brand’s values. This step often involves a delicate balance between performance and price, making it crucial to explore a variety of sources and suppliers.
In the context of manufacturing in China, the abundance of material options presents both an opportunity and a challenge. Engaging with suppliers who can provide detailed documentation and certifications for their raw materials ensures transparency and reliability. This scrutiny aids in verifying that the materials are ethically sourced and meet environmental standards, which is increasingly important to consumers worldwide. Additionally, consider how the choice of materials might affect the manufacturing process itself. Some materials may require specialized equipment or processes, potentially impacting production timelines and costs.
5. Secure Your Intellectual Property
In the realm of global manufacturing, particularly when partnering with factories in China, safeguarding your intellectual property (IP) is paramount. If your product has unique and novel features, consider filing for a patent to protect your design from being copied. This endeavor is vital to preventing unauthorized reproduction or imitation of your innovation.
Also, engaging in comprehensive agreements that cover nondisclosure and noncompete clauses with all parties involved, from suppliers to manufacturers, is crucial. These legal instruments act as a deterrent against IP theft, offering a layer of security for your product during its production journey.
6. Set Up Tooling and Equipment
The transition to mass production demands meticulous planning for tooling and equipment setup. This phase is crucial as it involves creating the molds, dies, and any custom machinery required to manufacture your product at scale. The design and fabrication of these tools must be precise, as they play a significant role in the efficiency of production and the quality of the final product. Working closely with your manufacturing partner to understand the specifications and limitations of their equipment is essential. It may also be necessary to invest in specialized tooling, which can be a significant upfront cost but is vital for achieving the desired output.
Additionally, the durability and maintenance needs of these tools should be considered, as they directly affect production continuity and costs. Engaging with experienced engineers and technicians who can optimize tool design for manufacturability can lead to significant savings in time and resources, reducing the per-unit cost of your product. This step also includes planning for the potential need to scale production up or down, ensuring that the tooling and equipment can be adapted to meet changing demands without sacrificing quality or incurring excessive costs.
Get Started with a Reliable Manufacturer in China
Moving from a concept to full-scale production is an exhilarating step for any entrepreneur. Preparing thoroughly before launching into mass production can save you time, money, and stress, ensuring that the product that reaches your customers is the best it can be.
If you are searching for a company that can handle all your production needs, consider Shield Works. We offer comprehensive services that range from industrial design and product development to contract manufacturing and product assembly. Our distinct advantage lies in our dedication to customization and exceptional customer service. We tailor each production plan to meet the unique requirements of our clients. For more details or to get assistance with preparing your product for mass production, contact us today!
Mastering Design for Manufacturing (DFM): A Guide to Efficient Production

In the evolving landscape of manufacturing, the imperative to streamline production processes and minimize costs is paramount. This is where Design for Manufacturing (DFM) plays a critical role. DFM is a proactive design approach aimed at simplifying manufacturing processes, reducing production costs, and ensuring product quality and consistency. In this comprehensive guide, we will explore what DFM entails, why it is crucial for manufacturers, and how it can be effectively implemented to achieve streamlined production outcomes. In today’s global market, manufacturing in China has become a key player, making it essential to understand how DFM can be applied in this context.
The Fundamentals of Design for Manufacturing
DFM, or Design for Manufacturability, is a general engineering practice of designing products in such a way that they are easy to manufacture. DFM hinges on the principle of designing products with the end goal of simplifying their manufacturing process, thereby making them more economical to produce. This strategy encourages the early integration of product design and manufacturing considerations, setting a foundation that significantly mitigates complexity, time, and cost associated with production.
At the core of DFM is the collaboration among product designers, engineers, and the manufacturing team, which is crucial for identifying and leveraging manufacturing capabilities and constraints from the outset. This collective effort ensures that each design decision takes into account the most efficient use of available resources, materials, and technologies.
The Importance of Design for Manufacturing
Design for Manufacturing (DFM) is a crucial engineering practice aimed at simplifying the design of products to optimize their manufacturing process. It plays a pivotal role in reducing production costs, enhancing product quality, and ensuring efficient manufacturing workflows. Here’s why DFM is so important:
Cost Reduction
DFM helps in identifying and eliminating unnecessary costs associated with materials, processing, and handling early in the design phase. By optimizing designs to use less expensive materials and more efficient fabrication methods, companies can significantly reduce the overall manufacturing cost.
Quality Improvement
When products are designed with manufacturing in mind, the resulting designs tend to be more robust and of higher quality. DFM encourages the use of proven production techniques and standard parts, which can improve the reliability and performance of the final product.
Speed to Market
Streamlining the design process for easier manufacturing can greatly accelerate production timelines. Faster prototyping, fewer revisions, and simplified assembly all contribute to a shorter time from concept to market. This can provide a competitive advantage in rapidly evolving industries.
Sustainability
Efficient designs often lead to reduced waste of materials and energy. DFM can enhance the sustainability of manufacturing processes by minimizing the ecological footprint of production, reducing waste and using resources more efficiently.
Reduced Complexity
Simplifying product designs makes them easier to assemble and reduces the likelihood of errors during the manufacturing process. This can decrease the need for skilled labor and reduce the incidence of defects or failures in the final product.
4 Key Strategies for Effective DFM Implementation
Effective Design for Manufacturability (DFM) implementation involves a set of strategies that streamline the manufacturing process. Here are key strategies to consider when implementing DFM:
Holistic Approach
For manufacturers aiming to successfully implement Design for Manufacturing (DFM), embracing a holistic approach from the onset of product design is critical. Integral to this is the early incorporation of manufacturing considerations, which ensures the design is inherently compatible with production capabilities and constraints. Utilizing Design for X (DFX) tools facilitates a multifaceted analysis, enabling designers to foresee and mitigate potential issues across various stages of production, such as assembly, testing, and maintenance. In parallel, adherence to Design for Assembly (DFA) guidelines promotes simplicity, advocating for designs that minimize part counts and complexity.
Collaboration
A collaborative spirit between the design and manufacturing teams is another cornerstone of effective DFM implementation. By fostering open lines of communication and promoting cross-functional team interactions, insights from the manufacturing floor can inform design decisions, ensuring that designs are not only innovative but also manufacturable at scale. This synergy between design and production personnel enriches the design process, enabling real-world manufacturing constraints and opportunities to shape the product from its conception.
Standardization
Using standard components and processes whenever you can is a smart move. Why? Well, standardization brings a bunch of benefits. First off, it can cut costs. Plus, it makes it easier to get what you need, reduces the stuff you have to keep in stock, and simplifies the training needed for putting things together and keeping them running smoothly.
Deploying Rapid Prototyping Technologies
Deploying rapid prototyping technologies offers tangible benefits, allowing teams to quickly evaluate the manufacturability of a design and adjust accordingly before full-scale production commences. This iterative approach reduces the risk of costly redesigns and ensures the final product can be manufactured efficiently, adhering to both cost and quality objectives.
Overcoming Common Challenges in DFM
Implementing Design for Manufacturing (DFM) is not without its hurdles. One significant obstacle is the inertia against altering established procedures and workflows, which can stall the adoption of DFM methodologies. Another issue is the siloed operation of design and manufacturing teams, which can hinder the seamless integration of DFM principles into the product development cycle. Additionally, a gap in comprehensive understanding of manufacturing processes among designers can further complicate the effective application of DFM.
Reshaping Manufacturing Possibilities with Shield Works
Design for Manufacturing is not just a cost-cutting tool; it’s a comprehensive strategy that enhances product quality, increases operational efficiency, and promotes sustainability. By integrating DFM principles into product design, companies can gain a competitive edge, respond more effectively to market changes, and achieve greater customer satisfaction.
If you’re interested in optimizing your product design and manufacturing processes, Shield Works is your go-to destination. We are a British-owned and managed company that specializes in high-quality contract manufacturing and product assembly services. Reach out today and discover how our expert DFM solutions can transform your product development lifecycle and enhance your competitive edge. Let’s work together to reshape the boundaries of manufacturing possibilities.
Navigating Supplier Agreement Management: Best Practices

Imagine how much further you can take your company’s performance when you work with the right supplier. You’ll avoid delays, develop stronger professional relationships, and save a substantial amount of money.
Navigating supplier agreement management can seem difficult at first. However, it’s essential for growing your business.
You will also avoid becoming one of the 20% of small businesses that fail within their first year. We’ve created a brief guide on how you can handle supplier agreements and find the ideal product supplier for your situation. Let’s explore the key information you need to know.
Engage with Key Stakeholders Early
Many businesses make the mistake of involving key stakeholders far too late in the process. This can lead to major complications, such as misalignment across different teams. In some situations, it can lead to delayed negotiations or broken agreements.
Instead, meet with the stakeholders before moving forward with your suppliers. This will help them understand compliance, financial, and data privacy requirements.
Overall, this process will make your relationship with your supplier far more fruitful. After involving stakeholders, ensure you update them on the current situation. This will help you avoid many potential issues you may have otherwise dealt with.
Establish Performance Expectations
Establish your goals at the beginning of your relationship with your supplier. Not only does this ensure everyone’s on the same page, but it also helps you weed out options that won’t meet your needs.
It’s worth noting that setting your expectations will help establish additional transparency. This is crucial for laying the foundation for strong professional relationships.
Have a Hub for Collaboration
Multiple teams should have a centralized location where they can access the required information. This allows stakeholders and suppliers to connect and get the information they need.
The last thing you want is to serve as the middleman between these two parties. This is inefficient and can detract from your other responsibilities.
Implement Outstanding Approval Workflows
Contracts are often stuck in limbo due to the need for approval. In many cases, the required party may have not even seen the agreement yet. Implementing approval workflows can help you get the signatures you need as soon as possible.
One of the best ways to expedite this process is by using automation. In context, this could involve an agreement automatically getting sent to the appropriate party after the previous user has taken action.
To further elucidate, imagine an employee at your organization approving a proposal from your supplier. This could then automatically be sent to them. Afterward, it will be returned once they provide their approval.
This maintains momentum and minimizes the chance of human error. Even a single incident could have major consequences. Keep this in mind when moving forward.
Regularly Review Your Agreements
Reviewing your agreements will provide valuable insight into key details. To clarify, your supplier agreement could have many upcoming deadlines. Missing even a single one can lead to major consequences.
After review, you can communicate with your team on how to handle upcoming obligations. Providing them with enough notice will help keep them productive and minimize their stress levels.
Cultivate Your Relationships
It’s not recommended to prioritize money over professional relationships. This can lead to you working with suppliers who don’t care about your company’s performance.
For example, you might find a supplier that allows you to easily stay within your budget. However, they may not have solid customer support.
They also don’t appreciate repeat business, making them unlikely to offer perks for renewed contracts. It’s best to find a product supplier you resonate with so you can focus on growing your relationship with them.
This is the added benefit of allowing you to save money in the future. It’s not uncommon for suppliers to give substantial discounts to their long-term clients. That might also provide you with other benefits, such as increased contract flexibility.
It can sometimes take years to forge a strong professional relationship, but it takes only seconds to undo it. Always stay communicative and respectful with your supplier. This will help you improve your company’s performance.
Finding the Right Supplier
The supplier you work with will heavily impact how easy it is to manage your agreements with them. It’s essential to do your due diligence before making your decision.
See what other people online have to say about the company’s performance. There should be no shortage of positive feedback praising their communication and professionalism. It’s also important to examine their pricing structure.
Not all suppliers are created equal, and you often get what you pay for when shopping around. For this reason, it’s never recommended to choose the cheapest options you find.
However, you don’t need to spend as much money as possible. Somewhere in the middle of the price range can help you reach your goals without stretching your budget. Do they seem enthusiastic about helping your company?
Never work with a business that isn’t passionate about bringing your vision to life. You can assess their enthusiasm by considering the questions they ask about your needs.
Do they have experience working with companies like yours? This is an attribute you can’t overlook, as it will help them understand your business’s unique nuances.
Ideally, you’ll find someone who’s been in the industry for at least a decade. With enough vigilance, you shouldn’t have an issue finding the best supplier for business growth.
Never Overlook Supplier Agreement Management
Without the right supplier agreement management place, you risk encountering major issues. These can derail your company’s trajectory.
The good news is that the information in this guide will help you make the best decisions for your future. Be sure to choose the right supplier, though.
Shield Works has provided customized OEM manufacturing, assembly, and warehousing solutions for almost two decades. We pride ourselves on our transparent, open, and flexible working practices.
We’re also 100% Western-owned, allowing us to have a strong understanding of your company’s goals. You can learn more about the benefits we provide when you speak with a representative today.
13 Benefits of Custom-Manufactured Products

In a world inundated with mass-produced goods, the allure of custom-manufactured products shines brighter than ever. These unique creations are tailored to individual preferences and needs.
It’s one of the many reasons why the global custom manufacturing market size is estimated to achieve a worth of $1,350.2 billion by 2031. Custom products also offer a myriad of benefits that extend far beyond their mere customization capabilities.
From enhancing functionality to fostering emotional connections, the advantages of opting for custom-made items are as diverse as they are compelling. This gives businesses a much-needed upper hand to stand out in a crowded marketplace.
Let’s delve into the world of bespoke manufacturing. Keep reading below to uncover remarkable benefits that come with custom products.
1. Custom-Manufactured Products Are Tailor-Made
Because custom-manufactured products are tailor-made products, they can be custom-designed to fit specific requirements. This ensures they meet the exact needs of the customer.
They are created with the customer’s unique preferences and specifications in mind, rather than being mass-produced for general use. This is important since 89% of products fail within their first 5 years due to a lack of customer understanding.
For example, no two people will wear the exact same size of suit. A tailor-made suit is crafted to fit the measurements and style preferences of the individual for a perfect fit and personalized look.
Likewise, this customization extends to include a wide range of products, such as parts, electronics, and machinery. By tailoring to specific needs, these products can offer better performance. They also offer increased comfort and improved functionality compared to off-the-shelf alternatives.
The design of these custom products provides a personalized and unique solution that meets the exact requirements of the customer.
2. Offers Unique Design
Custom-manufactured products offer unique designs. Having a unique design helps businesses stand out among a sea of mass-produced items.
These designs are then meticulously developed to match customer requirements and specifications. In doing so, it ensures a truly distinctive product.
Precision manufacturers can create custom parts or components with unique shapes, sizes, or features that are not available off the shelf. This uniqueness helps to differentiate a brand or product line. A unique design makes it more appealing to customers seeking something special.
Additionally, the ability to create custom designs allows for greater creativity and innovation. It leads to products that are not only functional but also visually striking.
The unique design aspect of custom-manufactured products adds value. By providing customers with a personalized and distinctive product that meets their specific needs and preferences, they enhance customer satisfaction and loyalty.
3. Allows for Quality Control
Custom manufacturing services allow for rigorous quality control measures to be implemented. Each product can be carefully inspected and tested to ensure it meets high standards.
This level of scrutiny is often not possible with mass-produced items. Quality control of mass-produced items may be more limited, resulting in inferior products.
By closely monitoring the production process, manufacturers can identify and rectify any issues early on. This ensures that the final product meets the customer’s expectations. This attention to quality control helps to build trust with customers, as they can rely on receiving a consistently high-quality product.
The ability to implement strict quality control measures is a key advantage of custom manufacturing. Implementing a quality control program leads to superior products and satisfied customers.
4. Provides Flexibility in Custom Goods
Custom-manufactured products provide flexibility in creating goods according to specific needs. It allows for adjustments according to customer needs like:
- Materials
- Sizes
- Shapes
- Colors
- Features
This flexibility means that customers can get exactly what they want made to their specifications rather than only picking from a selection of pre-made items.
For example, a customer can request a specific color, size, or material for a product, which may not be available in standard, mass-produced items. Additionally, custom manufacturing enables quick adjustments to be made during the planning and production process as needed. This ensures that the final product meets the customer’s expectations.
The flexibility that comes with custom-manufactured products allows for greater customization and personalization. It leads to products that better meet the needs and preferences of customers.
5. Facilitates Cost-Effectiveness
Custom manufacturing facilitates cost-effectiveness. It optimizes production processes to improve efficiency. Each product is made to order, eliminating the need for excess inventory and storage costs.
Additionally, custom manufacturing allows for the use of materials that are specifically tailored to the product’s requirements. This also reduces material costs. By producing only what is needed, manufacturers can also reduce labor costs and overhead expenses.
Furthermore, custom manufacturing can lead to products that are more durable and efficient. It reduces the need for frequent replacements or repairs which can be costly and stunt business growth. This enables you to create a high-quality product that meets the exact needs of the customer.
The initial costs associated with custom-manufactured products may be higher than mass-produced alternatives at first. However, the cost-effectiveness of custom manufacturing stems from its ability to streamline production processes.
6. Reduces Waste
Custom manufacturing reduces waste by producing goods only when there is demand. This eliminates the need for excess inventory that could become obsolete or go unsold. Since custom-manufactured products are made to order, there is less likelihood of overproduction, which can lead to additional waste.
Furthermore, custom manufacturing allows for the precise planning of materials. This reduces the likelihood of leftover or unused materials. Manufacturers can also use materials more efficiently by tailoring them to the specific requirements of each product to minimize waste.
The customization aspect of custom manufacturing allows for products to be designed with longevity and durability in mind. This means that customers are more likely to keep and use their custom-made products for longer periods. It helps reduce the overall amount of waste generated by frequent replacements or disposals.
By reducing waste, custom manufacturing helps to lower costs associated with disposal and environmental impact. The waste reduction benefits of custom manufacturing contribute to a more efficient production process.
7. Delivers Environmental Benefits
Sustainability and eco-friendliness are at an all-time high among consumers. A PwC Global Consumer Insights Poll from June of 2023 confirms it. Their survey found that more than 70% of consumers polled said they were willing to pay more for sustainably produced goods.
Custom manufacturing allows for the use of sustainable materials and production methods. Manufacturers can choose materials that are eco-friendly and recyclable. This minimizes the environmental impact of their products.
Utilizing custom-manufactured products delivers environmental benefits by reducing waste and energy consumption. Since products are made to order, there is less need for excess inventory that could end up in landfills. This also reduces the energy required for transportation of unused goods.
With custom manufacturing services, there is often a more efficient use of resources. Manufacturers can optimize production processes to minimize waste and energy consumption. In turn, this leads to a smaller carbon footprint overall.
8. Improves Product Functionality
Custom manufacturing improves product functionality by tailoring products to meet specific needs and requirements. This means that each product can be specifically designed with features and capabilities that are not available in standard, mass-produced items.
Take for instance, a custom-built computer that comes configured with the exact specifications needed for a particular use case, such as gaming or graphic design. Custom-manufactured products allow for the incorporation of innovative technologies and materials that can enhance product performance.
An example of this could include the use of lightweight and durable materials in aerospace components. Another example may include the integration of advanced sensors and software in medical devices.
The ability to customize products leads to improved functionality and performance. It makes them more effective in meeting the needs of customers.
9. Enhances Branding Efforts
Creative and innovative product designs can generate buzz and excitement around the brand. Custom manufacturing enhances branding efforts by providing unique products that reflect the brand’s identity.
Custom-made products can be designed with specific elements that align with the brand’s image such as:
- Colors
- Logos
- Features
- Materials
- Packaging
These aspects help reinforce brand recognition and loyalty. Color alone is responsible for as much as 80% of brand recognition. It also evokes specific emotions.
Additionally, the ability to offer custom products sets a brand apart from competitors. It showcases a commitment to quality and customer satisfaction.
Effective branding can attract new customers who are looking for personalized products. It can also help retain existing customers who value the brand’s attention to detail. This can lead to increased brand visibility and awareness for business growth.
10. Elevates Customer Experience
Custom manufacturing elevates the customer experience. One way it accomplishes this is through custom-crafted products. This customization allows customers to have a more personal and meaningful interaction with the brand and enhances their overall satisfaction.
Additionally, the ability to customize products creates a sense of exclusivity and uniqueness. This makes customers feel special and valued. It can lead to stronger customer loyalty and positive word-of-mouth referrals.
Using custom manufacturing enables customers to be actively involved in the design process. It lets them express their creativity and individuality. Offering an interactive experience can deepen the connection between the customer and the brand.
The elevated customer experience provided by custom-manufactured products can lead to increased customer satisfaction and long-term loyalty. In essence, it fosters a sense of ownership and pride in the final product.
11. Delivers a Quick Turnaround
Despite its custom nature, custom manufacturing can deliver a quick turnaround. It does so by streamlining production processes and focusing on individual orders.
Since products are made to order, there is no need to wait for inventory restocking or for items to be shipped from a warehouse. This means that customers can receive their products much faster. Often this can take a matter of days or weeks, depending on the complexity of the order.
Custom manufacturing allows for efficient scheduling of production runs. This process minimizes downtime and delays. Manufacturers can prioritize orders based on urgency to ensure that important orders receive the quickest completion.
The use of advanced technology and automation processes can further speed up the production process for even quicker turnaround times. These quick turnaround times help to meet customer deadlines and expectations. This leads to higher overall customer satisfaction.
12. Boosts Efficiency
Efficiency in business is paramount. Whether it’s across the U.S. or the globe, business growth depends heavily on how efficiently resources are utilized. The efficiency gains from custom manufacturing help manufacturers reduce costs.
Custom manufacturing services optimize production processes for each individual order. This allows for a more streamlined and cost-effective operation. It enables the delivery of high-quality products to customers in a timely manner.
Advanced technologies and automation further enhance efficiency. This includes the use of computer-aided design (CAD) software, robotics, and advanced machinery to streamline production processes and improve accuracy.
The customization aspect enables manufacturers to tailor their processes to meet the specific needs of each order. This can include adjusting production schedules and optimizing material usage. It also helps implement quality control measures that are specific to each order.
13. Increases Productivity
Optimizing production processes to meet the specific needs of each order increases productivity. This means that manufacturers can produce goods more efficiently. In effect, it reduces the time and resources required for production.
Custom manufacturing allows for the use of advanced technologies and automation to further enhance productivity. This includes the use of robotics and computer-aided design (CAD) software. The use of advanced machinery streamlines production processes and improves output.
Through customization, manufacturers can prioritize orders based on urgency. This ensures the completion of the most important orders first. It also helps to maximize output and minimize downtime for higher overall productivity.
The productivity gains from custom manufacturing help manufacturers to produce more goods in less time. It leads to increased profitability and business growth.
Redefine Your Manufacturing Services with Shield Works Precision Manufacturing Today
Offering custom products is a smart strategy for business growth. Custom-manufactured products help you stand out in a competitive market, attract customers, and build brand loyalty. If you’re having difficulty hiring a manufacturer that works for your business needs, you need Shield Works.
Shield Works is a British-owned and operated manufacturer located in Zhuhai, China. We offer quality assembly, warehouse, and OEM manufacturing services. With nearly two decades of expertise in the manufacturing industry, you can trust our on-time delivery, transparency, and quality standards.
Interested in growing your business? Contact us today for more information and we’ll respond within 24 hours.
Avoiding the Pitfalls of Outsourcing Manufacturing: The Key to Clear Specifications in China

Outsourcing manufacturing to China offers a multitude of benefits, including cost reduction, access to a vast manufacturing infrastructure, and a speedy production timeline. However, navigating the process isn’t without its challenges, particularly when it comes to communication.
Misunderstandings, cultural differences, and discrepancies in standards can significantly impact the quality of the final product, induce delays, and inflate costs. To sidestep these obstacles, it’s imperative to establish clear, detailed, and unambiguous specifications from the outset. In this blog post, we delve into strategies to avoid miscommunication and ensure a smooth manufacturing process in China.
Importance of Clear and Detailed Product Specifications
Crafting crystal-clear specifications is fundamental when engaging with Chinese manufacturers. This critical step transcends mere lists of dimensions or material types; it encompasses exhaustive technical documentation, precise material characteristics, defined quality expectations, packaging guidelines, and any supplementary details that influence the product’s outcome.
The goal is to eliminate ambiguity, ensuring that every aspect of the product is thoroughly understood. Incorporating visuals, such as technical drawings or prototypes, is advisable to further close any communication gaps. Such meticulous attention to detail in the specification phase greatly reduces the likelihood of errors, aligning the manufacturing process more accurately with your envisioned product. This meticulousness is not just about avoiding mistakes; it’s about setting a clear roadmap that guides every step of the production journey, ensuring that the finished goods mirror your exact requirements. Engaging in this level of detail demands time and effort, but it is a pivotal investment that pays dividends in reducing misinterpretations and ensuring that your product emerges from the manufacturing process as you intended.
Effective Strategies When Outsourcing Manufacturing to China
To circumvent misunderstandings when outsourcing manufacturing to China, it’s critical to engage in proactive and consistent communication. Here are some key strategies to achieve this:
Detailed Product Specifications
Provide comprehensive and detailed product specifications. This includes materials, dimensions, tolerances, colors, and any other relevant details. The more detailed your specifications, the less room there is for interpretation.
Technical Drawings and Samples
Along with written specifications, provide technical drawings and, if possible, physical samples. This helps to bridge any language barriers and ensures that the manufacturer has a concrete example to work from.
Understanding of Local Practices
Familiarize yourself with Chinese manufacturing practices and standards. There can be differences in material standards, measurements, and quality expectations. Knowing these can help in setting realistic and clear specifications.
Effective Communication
Establish a clear line of communication with your manufacturer. This often means having someone on your team who speaks Mandarin or hiring a local agent or intermediary who can bridge the language and cultural gap.
Regular Visits and Inspections
If possible, visit the manufacturing site regularly. This allows you to build a stronger relationship with the manufacturer, inspect the production process, and address any issues in real-time. If you can’t visit, consider hiring a local inspection company.
Prototyping and Samples
Before going into full production, have a prototype or sample batch produced. This allows you to check that the manufacturer has understood and can meet your specifications before you commit to a larger order.
Contract Clarity
Make sure your contract clearly outlines product specifications, quality requirements, timelines, and penalties for non-compliance. A well-defined contract can provide a strong basis for resolving any disputes.
Preparing for and Managing Potential Delays
In the landscape of manufacturing in China, anticipating and managing potential delays is critical for maintaining a seamless production schedule. It’s essential to incorporate a strategic buffer in your project timelines to absorb any unexpected setbacks. Active and ongoing communication with your Chinese manufacturing partner is key to staying ahead of any issues that might affect production. This approach allows for real-time adjustments and ensures that both parties are aligned on expectations and timelines.
Developing a comprehensive understanding of the Chinese manufacturing calendar, including public holidays and peak production periods, can help in forecasting and planning for times when delays are more likely. Implementing contingency strategies is also prudent. These could involve identifying alternate suppliers or logistics options that can be activated if the need arises.
Regularly revisiting and updating your production and delivery schedules with your manufacturer can also play a significant role in mitigating delays. This practice encourages proactive problem-solving and adjustment of timelines as needed, based on the latest information and production realities. By adopting these measures, businesses can navigate the complexities of manufacturing in China more effectively, ensuring that timelines are realistic and flexible enough to accommodate the unpredictable nature of production and shipping processes.
The Path to Successful Outsourcing in China
Navigating the complexities of outsourcing manufacturing to China necessitates a comprehensive and proactive approach. While the journey may present challenges, the strategic benefits—cost efficiency, scalability, and tapping into a robust manufacturing ecosystem—are compelling. A thoughtful, informed strategy is key to unlocking these advantages, transforming potential obstacles into stepping stones for successful international manufacturing endeavors.
If you’re considering outsourcing your production project to a reliable manufacturer, look no further than Shield Works. Shield Works stands out in the crowded field of contract manufacturing with its unique blend of Western management practices and deep understanding of the Chinese manufacturing landscape. This combination ensures that our clients receive not only the cost benefits associated with manufacturing in China but also the quality and reliability expected by Western markets.
At Shield Works, we understand that communication is key to successful outsourcing. We offer a transparent and seamless communication process, ensuring that our clients are always informed and in control. Our bilingual team bridges the language and cultural gap, facilitating smooth interactions and ensuring that your specifications and expectations are clearly understood and met. Contact us today and let us handle the complexities of manufacturing so you can focus on growing your business.
Ways to Keep Your Manufacturing Production and Assembly Competitive

Every minute your production line isn’t optimized, you’re losing ground to competitors. In the fast-paced world of manufacturing, staying ahead means constant adaptation and improvement.
Whether you oversee a small product assembly workshop or a large-scale contract manufacturing operation, the stakes are high. Keeping up with production and assembly demands is crucial. As markets evolve and customer preferences shift, your approach to manufacturing must also transform.
This guide offers practical strategies to boost your production and assembly efficiency. From cutting costs to enhancing output, the tips provided here will help you maintain a competitive edge. Dive into the world of efficient manufacturing and discover how to keep your operations lean and powerful.
Understand Your Market Demand
You need a crystal-clear picture of what your customers want. Aligning your manufacturing and assembly processes with market demand streamlines operations. It also reduces waste.
Regular market analysis keeps you ahead of trends and prepares you for shifts in consumer preferences. Understanding these needs ensures you’re not overproducing or holding excess inventory.
Excess inventory ties up capital and decreases efficiency. Tailoring your product lines to specific market demands enhances customer satisfaction and loyalty.
These are critical for sustained business success. Stay informed by attending trade shows, engaging directly with customers, and monitoring competitor activities. These actions help you make decisions that align your operations with market needs.
Forge Strong Supplier Relationships
Strong partnerships with suppliers can make or break your efficiency. Working closely with suppliers gives you insights into material availability. Plus, it helps you negotiate better prices or favorable terms.
Regular communication prevents delays and ensures a steady supply chain. Build relationships based on trust and mutual benefit. This approach often leads to better service and beneficial innovations.
Consider long-term contracts to secure lower prices and ensure supply consistency. This strategy can give you a competitive edge.
Diversifying your supplier base avoids disruptions and reduces risks associated with single suppliers. Effective supplier management not only streamlines your production process but also enhances the quality and reliability of your products.
Emphasize Quality in Contract Manufacturing
In contract manufacturing, your reputation hinges on quality. Investing in high-quality materials and advanced training for your staff leads to fewer defects and returns. These investments save money in the long run and bolster your brand’s reputation.
High standards in production ensure customer satisfaction and repeat business. Prioritize quality control at every stage of production, from sourcing raw materials to the final assembly. Regular audits and checks maintain these high standards.
Implementing stringent quality assurance practices can reduce downtime and minimize waste. This commitment to excellence positions your business as a reliable and superior partner in a competitive market.
Optimize Your Product Assembly Line
Revamping your product assembly line can lead to significant gains in speed and efficiency. Consider layout changes that reduce movement and streamline operations.
Introduce automation where it offers the most return on investment. A good place to start is with repetitive, labor-intensive tasks. Each improvement can shave seconds off assembly times, and over time, these seconds add up to substantial benefits.
Analyze workflow processes to identify bottlenecks and address these areas with targeted improvements. Simple changes could include reorganizing workstations or upgrading to more efficient machinery. You might be astounded by how you can dramatically increase output and reduce labor costs when doing such things.
Continuous evaluation and adjustment of the assembly line keep your production process agile and responsive to changing market demands.
Keep Manufacturing Costs in Check
Monitor your manufacturing costs relentlessly. Identify areas where you can cut expenses without compromising quality. This might involve:
- Adopting new technologies
- Renegotiating supplier contracts
- Streamlining your product designs for easier assembly
Efficient cost management is crucial for maintaining profitability. By scrutinizing every aspect of your expenses you can uncover opportunities for significant savings. For example, you can look at energy usage and material waste.
Implementing cost-effective strategies like bulk purchasing or using energy-efficient machines also helps reduce overheads. Staying proactive in cost management enables you to offer competitive pricing. And you can do this while maintaining healthy margins.
Utilize Lean Manufacturing Principles
Lean manufacturing focuses on minimizing waste within manufacturing systems while maximizing productivity. Implementing these principles can help you create more value with fewer resources. This is essential for staying competitive.
Start by mapping out all your processes to identify unnecessary steps that do not add value to the end product. Once identified, work on eliminating these inefficiencies.
Training your team on lean principles is crucial. It ensures everyone understands the importance of reducing waste and improving workflow.
Regularly revising and refining processes based on lean methodologies can lead to continuous improvements and significant cost savings. This approach not only streamlines production. It also enhances product quality and customer satisfaction.
Continuous Training and Development
Your workforce is your biggest asset. Regular training ensures that your employees are more efficient and better equipped to handle the nuances of modern manufacturing and assembly lines. Investing in your team is investing in your company’s future.
Simple, ongoing training programs can teach new skills and refine old ones, keeping your staff updated with the latest industry standards and technologies. These initiatives boost morale and productivity, leading to a more capable and satisfied workforce.
Offer both technical training and soft skills development to cover all aspects of your employees’ roles. This comprehensive approach ensures that your team can meet challenges head-on and adapt to any changes in the manufacturing landscape.
Enhanced skills lead to improved productivity and innovation. These are crucial for maintaining a competitive edge in today’s fast-moving manufacturing environments.
Harness Technology for Better Efficiency
Technology can be a game-changer in manufacturing and assembly. From automated assembly lines to real-time data analytics, the right technological tools can enhance your operations dramatically.
Look into adopting systems that integrate seamlessly into your existing processes to boost efficiency. For example, using robotics for repetitive tasks not only speeds up production but also reduces human error. Implementing software for inventory management can help track materials accurately and streamline the supply chain.
Additionally, consider using advanced data analytics. With it, you can monitor machine performance and predict maintenance needs before breakdowns occur.
Staying updated on new technologies that could disrupt your industry or provide new opportunities for growth is crucial for maintaining a competitive advantage. Embracing these innovations can transform your production processes, making them:
- Faster
- More efficient
- More responsive to market demands
Focus on Sustainability
More consumers and businesses are valuing sustainability. By integrating eco-friendly practices into your production processes, you can attract new customers and reduce environmental impact.
This could mean anything from recycling waste materials to using renewable energy sources. Simple steps like switching to energy-efficient lighting or reducing packaging waste make a big difference.
These changes help the planet and often reduce costs in the long run. Becoming known as a sustainable business can also set you apart from competitors, attracting customers who are conscious about the environment.
Evaluate and Iterate
Regular evaluation of your processes helps you spot issues before they become major problems. Use data to drive your decision-making and continually refine your operations. This commitment to improvement will keep you competitive in a tough market.
Start by gathering feedback from all levels of your workforce. They can provide insights into what works and what doesn’t. Also, regularly check your machinery and systems to ensure they are working efficiently.
Making small adjustments based on your findings can lead to big improvements over time. Keep looking for ways to do things better and make those changes.
Flexibility in Production and Assembly
Being flexible in how you manage production and assembly helps you respond quickly to changing conditions. Whether adapting to new market demands or scaling operations up or down, flexibility is a significant competitive advantage.
Keep your processes adaptable so you can adjust swiftly when needed. For example, if a particular product becomes very popular, you should be able to increase production quickly.
Conversely, if something isn’t selling well, you should be able to reduce output efficiently without incurring significant costs. This level of flexibility ensures you remain efficient and responsive, crucial traits in today’s fast-evolving market.
Stay Ahead of Regulations
Manufacturing is often heavily regulated. Staying on top of relevant regulations and compliance requirements prevents costly fines and delays, enhancing your company’s reputation as a reliable and trustworthy manufacturer.
Make it a priority to understand the laws and standards that affect your industry. Regularly train your staff on these regulations to ensure everyone is compliant.
Keeping up with regulations ensures your operations are legal and safe. It also demonstrates to your customers and partners that you are committed to quality and safety. This proactive approach can strengthen your market position and build trust with your stakeholders.
Streamline Logistics
Efficient logistics are vital to keeping your production and assembly lines running smoothly. Improving your logistics can reduce lead times and lower costs. This gives you an edge over competitors who struggle with distribution.
Focus on optimizing your transportation routes and warehouse management practices. Implementing software solutions that manage inventory and track shipments in real time can also enhance efficiency.
Regularly review and adjust your logistics strategies to better align with production schedules and market demands. This proactive approach to logistics ensures that your products are delivered on time. Plus, it minimizes storage and transportation expenses.
Enhance Process Automation
Increasing the level of automation in your manufacturing processes can significantly boost efficiency and consistency. Consider areas in your production line that are repetitive and prone to human error for automation opportunities.
Installing automated machinery can speed up these processes while maintaining high quality. For instance, robotic arms can perform precise tasks faster and with fewer errors than manual labor.
Additionally, automated systems can work around the clock, increasing production capacity without the need for overtime costs. When you integrate more automation, you can:
- Reduce labor costs
- Increase output
- Maintain a competitive edge in your industry
Monitor and Manage Energy Usage
Effective energy management is crucial for reducing operational costs and enhancing the sustainability of your manufacturing operations. Identify areas where energy consumption is high and explore ways to reduce it.
This might involve:
- Upgrading to energy-efficient machinery
- Optimizing heating and ventilation systems
- Implementing smart sensors to monitor and control energy use
By reducing energy consumption, you not only cut costs but also contribute to environmental sustainability. Regular audits and continuous monitoring of energy usage help ensure that your manufacturing processes are as energy-efficient as possible. Indeed, this can significantly impact your bottom line and environmental footprint.
Develop Strong Industry Partnerships
Cultivating strong partnerships within your industry can provide numerous benefits, including:
- Shared resources
- Knowledge exchange
- Collaborative innovation
Establish connections with other manufacturers, technology providers, and industry experts to stay abreast of emerging trends and technologies. These relationships can lead to joint ventures or partnerships that leverage collective strengths. We’re talking about strengths such as co-developing new products or sharing distribution networks.
The idea is to work closely with industry peers, then you can:
- Gain insights into best practices
- Improve your operational efficiency
- Create new growth opportunities
Prioritize Customer Feedback
Listening to your customers is key to staying competitive in manufacturing. Prioritize gathering and analyzing customer feedback to better understand their needs and expectations.
Use surveys, direct interviews, and social media interactions to collect valuable insights. This feedback can guide your product development, help you adjust your production processes, and improve overall customer satisfaction.
If you respond to customer needs and make necessary adjustments, you demonstrate your commitment to quality and service. This should help you retain existing customers. Plus, you’ll be able to attract new ones through positive word-of-mouth.
Production and Assembly Insights
Your ability to adapt and innovate in production and assembly determines your competitiveness. Keep pushing for efficiency and quality, and you’ll set your business up for success.
At Shield Works, we specialize in customized OEM manufacturing, assembly, and warehousing solutions tailored for our international clients. With 19 years of experience in China, our expert team delivers high-quality products from secure, IPR-protected zones.
Contact us to enhance your supply chain with our risk-free, transparent, and flexible manufacturing solutions.
Revolutionizing Manufacturing: How Comprehensive Quality Inspections Elevate Your Process

In the fast-paced world of manufacturing, the importance of quality cannot be overstated. As industries evolve and consumer demands increase, the need for rigorous quality inspections has become more critical than ever. Comprehensive quality inspections are not just about catching defects; they are about fundamentally transforming manufacturing processes to boost efficiency, enhance product quality, and exceed customer expectations. This blog explores how incorporating thorough quality checks can revolutionize your manufacturing operations.
Understanding Comprehensive Quality Inspections
Comprehensive quality inspections involve an extensive examination of products at various stages of the manufacturing process. Unlike traditional methods that focus on end-product evaluation, comprehensive inspections are integrated throughout the production cycle. This proactive approach helps in identifying and resolving issues before they escalate, ensuring that the final product meets the highest standards of quality.
Key Components of Comprehensive Inspections
- Material Inspection: Assessing raw materials before production to ensure they meet required specifications.
- In-Process Inspection: Continuous checks during manufacturing to monitor and control the process.
- Final Product Inspection: Detailed examination of finished products to confirm overall quality and functionality.
- Packaging Inspection: Ensuring packaging meets set standards to protect the product during transportation and storage.
The Impact of Quality Inspections on Manufacturing Efficiency
Incorporating comprehensive inspections can dramatically enhance manufacturing efficiency. By catching defects early, manufacturers can reduce wastage and save on costs associated with reworking or scrapping defective products. Moreover, systematic inspections streamline production processes by integrating quality control as a fundamental component, rather than treating it as an afterthought.
Reduced Downtime
One of the primary efficiency benefits is significantly reduced downtime. Quick identification and correction of issues are crucial in preventing lengthy disruptions in operations. With diagnostic tools and real-time monitoring technologies, businesses can swiftly detect and address malfunctions or inefficiencies, ensuring that production processes are not halted for extended periods. This rapid response capability not only minimizes financial losses associated with halted production but also improves overall workflow continuity.
Optimized Production
Enhanced process control is another key benefit that leads to optimized production. By integrating sophisticated control systems and automation technologies, manufacturing processes become more precise and less prone to human error. This results in a more consistent and reliable output, enhancing product quality. Moreover, optimized production processes can adapt more efficiently to changes in demand and specifications, allowing for flexibility and scalability in operations. This level of control ensures that every aspect of the production line is fine-tuned to operate at peak efficiency.
Resource Conservation
Efficient use of resources is fundamental to achieving more sustainable manufacturing practices. By minimizing material wastage, businesses not only reduce their operational costs but also contribute to environmental conservation. Advanced manufacturing technologies enable precise calculations and material handling, which drastically cut down on waste. Additionally, improved process efficiency often leads to reduced energy consumption, further enhancing the environmental sustainability of manufacturing practices. This conscientious approach to resource management not only supports global sustainability efforts but also aligns with the growing consumer demand for environmentally responsible products and practices.
Enhancing Product Quality and Compliance
Quality inspections are crucial for not only maintaining but also enhancing product quality. They ensure that every product that leaves a facility meets the required standards and regulations, which is vital in industries such as pharmaceuticals, automotive, and food and beverage. Compliance with legal standards and safety regulations protects companies from potential lawsuits and recalls, which can be costly and damaging to a brand’s reputation.
Meeting Industry Standards
To remain competitive and compliant, it’s crucial for businesses to ensure that their products meet specific industry standards and regulations. This involves rigorous testing and quality assurance processes to match or exceed the criteria set by industry bodies. Successfully meeting these standards not only prevents legal issues and fines but also strengthens the marketability of the product by affirming its quality and safety.
Enhancing Customer Trust
When a company consistently delivers reliable products, it builds a strong foundation of trust with its customers. This trust is essential for fostering customer loyalty and can significantly enhance the reputation of the brand. High-quality, dependable products lead to increased customer satisfaction, which in turn encourages repeat business and positive word-of-mouth, crucial elements for long-term success.
Global Market Access
Adhering to international standards and regulations is not just about compliance—it’s a strategic move that opens up numerous opportunities for business expansion into new markets. By ensuring products meet these global standards, companies can tap into international markets more easily, overcoming barriers to entry and competing on a global scale. This compliance not only broadens the customer base but also diversifies business risks.
Enhancing Product Quality with Expert Inspection Services
Quality inspections in the manufacturing sector are not just a step in the process; they represent a comprehensive strategy that significantly improves the entire manufacturing workflow. This approach goes beyond simply ensuring that products meet certain standards. It involves a detailed examination of every stage of the manufacturing process, from the sourcing of raw materials to the final delivery of the product, ensuring that each phase adheres to the highest quality standards. By identifying defects and non-conformities early in the production cycle, you can mitigate risks, enhance safety, and avoid costly recalls and repairs.
Thoroughness in Inspection Protocols
Effective inspection services rely on comprehensive protocols that cover every stage of the production process, from raw materials to final products. Inspectors use a variety of methods and tools, such as visual examinations, non-destructive testing techniques, and advanced automated systems to identify potential issues that could affect product quality.
Integration with Production Processes
Inspection services should not function as a separate entity but should be integrated into the production process. This integration allows for real-time feedback and swift action to correct any deviations from the quality standards. It also fosters a culture of quality awareness throughout the organization, making quality everyone’s responsibility.
Compliance and Certification Support
Expert inspection services are not only about identifying defects but also ensuring compliance with national and international standards. Professional inspectors are knowledgeable about regulatory requirements and can help companies navigate the complex landscape of certifications, which is crucial for accessing global markets.
Partner with A Reliable Quality Inspection Company
Incorporating expert inspection services into your production process is not merely an operational decision; it’s a strategic one. Are you ready to take your product quality to the next level? Our team at C2W is ready to be your committed local partner in this journey.
At C2W, we employ a team of seasoned experts who utilize the latest methodologies to conduct comprehensive inspections throughout your production process. Our approach is meticulously tailored to meet the unique needs of your business, ensuring that the solutions we offer are not only effective but also innovative. By partnering with us, you gain access to a wealth of expertise in quality control and assurance. We are committed to helping you achieve not just compliance with industry standards, but a level of quality that sets you apart in the marketplace. Reach out to us to learn more about how our quality inspection services can transform your manufacturing process, leading to enhanced product quality, increased efficiency, and a stronger bottom line.
OEM vs ODM: Navigating the Manufacturing Maze
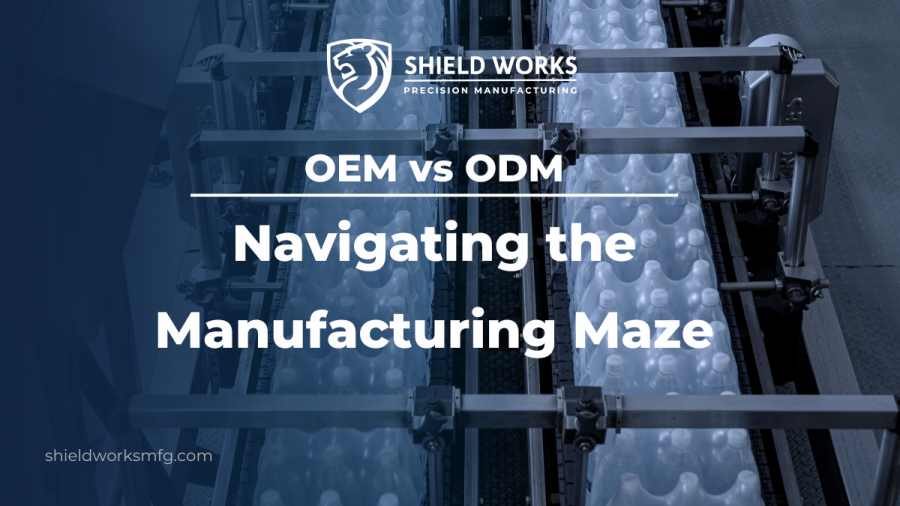
Navigating the manufacturing maze often involves understanding various industry terms and concepts, particularly when it comes to OEM (Original Equipment Manufacturer) and ODM (Original Design Manufacturer). These terms are crucial in the world of product development and manufacturing, especially for businesses looking to outsource these aspects. Understanding the differences between OEM and ODM, as well as their respective advantages and disadvantages, is essential for making informed decisions in the manufacturing process. This comprehensive guide will navigate you through the OEM vs ODM manufacturing maze, helping you make informed decisions that align with your business goals.
Understanding OEM and ODM
What is OEM?
OEM stands for Original Equipment Manufacturer. This term refers to a company that manufactures products or components that are purchased by another company and retailed under the purchasing company’s brand name. OEMs typically work based on the buyer’s design specifications.
Example: A good example is a company that makes computer processors (like Intel or AMD) which are then used in various brands of computers. The computer brands are the clients of the processor manufacturers.
What is ODM?
ODM stands for Original Design Manufacturer. This type of company designs and manufactures a product that is eventually branded and sold by another firm. ODMs provide both design and production services, offering a complete package from product concept to finished goods.
Example: A common example is in the electronics sector, where an ODM might design and manufacture a range of smartphones or gadgets that are then branded and sold by another company.
Key Differences Between OEM and ODM
Understanding the differences between OEM and ODM is crucial in selecting the right manufacturing partner. Here are some key distinctions:
Design Ownership
In an OEM arrangement, the client company retains full ownership of the product design. This means they provide the specifications and blueprints for the product they want to be manufactured. The OEM partner is responsible for producing the product according to these specifications. This level of control allows the client to ensure that the product meets their exact requirements and quality standards.
In contrast, with ODM, the manufacturing company not only produces but also designs the product. The design rights belong to the ODM. Clients choosing an ODM partner typically select from a range of existing product designs and may have some room for minor modifications. However, the core design and technology remain the property of the ODM.
Cost Implications
Opting for OEM manufacturing can be more expensive. This is because creating a product from scratch, with specific design requirements, often involves extensive research and development, as well as the need to create specialized molds or tools. These initial investments can add to the overall cost of the product.
ODM solutions can be more cost-effective, particularly for businesses looking to enter the market with a lower investment. Since ODMs use their existing designs and production processes, the costs associated with design and development are significantly reduced. This can be a more economical option for companies that do not require highly customized products.
Time to Market
The time to market can be longer in OEM arrangements due to the need for custom design and development processes. This includes time for prototyping, testing, and potential redesigns, which can extend the time before the product is ready for launch.
ODM manufacturers typically offer quicker turnaround times. Since they are working with pre-existing designs and have experience in mass-producing these designs, they can modify and produce products more rapidly. This can be a crucial advantage for companies looking to capitalize on market trends or seasonal demands.
Customization Level
OEM is ideal for companies that require high levels of customization. Since the client controls the design, they can specify every aspect of the product, from materials and components to the final appearance and functionality. This is particularly important for companies with unique product requirements or those operating in niche markets.
ODM offers limited customization. The modifications are generally restricted to aspects like branding, color schemes, and minor feature changes. This is suitable for businesses that are satisfied with existing product designs and do not need extensive alterations.
Intellectual Property
In an OEM partnership, intellectual property concerns are typically more straightforward. The client company, owning the design, retains the IP rights. This clear delineation can provide a sense of security and is crucial for companies whose value is tied to their proprietary designs and technology.
IP rights in an ODM arrangement can be more complex. Since the design belongs to the manufacturer, the client needs to negotiate the terms of use, including where and how the product can be sold, and any exclusivity arrangements. Understanding and negotiating these terms is critical to avoid potential legal issues and to ensure that the client’s interests are protected.
Choosing Between OEM and ODM
When faced with the decision of selecting between OEM and ODM for product development and manufacturing, various critical factors come into play. Here’s an expanded view of these considerations:
Nature of the Product
This approach is ideal for highly specialized or innovative products. If your product requires specific design, unique features, or proprietary technology, OEM allows for greater customization and exclusivity. In OEM, the manufacturer builds the product based on your exact specifications, ensuring that your vision for a unique product is realized.
On the other hand, ODM is suitable for more generic or standard products. If your product does not demand unique specifications and can be adapted from existing designs, ODM is a practical choice. ODM manufacturers offer their designs and products, which you can rebrand and sell. This is particularly beneficial if the product is common and does not require significant differentiation in the market.
Budget Constraints
Generally, OEM requires a higher investment due to the need for custom design, development, and tooling. If your budget allows for these expenses and the expected ROI justifies the initial costs, OEM can be a worthwhile investment.
For businesses with tighter budget constraints, ODM is often more cost-effective. Since the product is already designed and tested by the manufacturer, the costs associated with design and development are significantly reduced. This makes ODM a popular choice for startups and small businesses looking to launch products without heavy upfront investments.
Market Strategy
If your market strategy revolves around brand uniqueness and creating a distinct product identity, OEM is the way to go. It allows for greater customization, enabling you to develop products that can be patented and stand out in the market. This is particularly important in industries where brand differentiation is a key competitive advantage.
If the strategy is to enter a market quickly with a product that does not necessarily need to be unique, ODM is more suitable. It allows companies to leverage existing market trends with products that are already popular, reducing the risk associated with market acceptance.
Time Constraints
The OEM process is typically more time-consuming, as it involves developing a product from scratch, including design, prototyping, and testing phases. If time to market is not a critical factor, and you can afford a longer development cycle, OEM allows for a tailored product development process.
For businesses looking to launch products quickly, ODM offers a significant advantage. Since the products are already developed and often just need rebranding, the time from concept to market is substantially shorter. This is particularly advantageous in fast-moving industries where being first to market can be crucial.
Quality Control
If maintaining strict quality control is vital, OEM provides more oversight and control over the manufacturing process. You can specify materials, components, and production methods, and have greater involvement in quality assurance processes.
While ODM still maintains a level of quality, the control over production is less compared to OEM. The designs and processes are predetermined by the manufacturer, which might not always align with your specific quality standards. However, for products where extreme customization is not required, ODM can still offer a reliable level of quality.
Best Practices in Partnering with OEMs and ODMs
The choice between OEM and ODM manufacturing depends on various factors. Each model offers distinct advantages and challenges, and the right choice varies based on individual business needs and goals.
Remember, the key to successful manufacturing lies not just in choosing between OEM and ODM, but also in selecting the right manufacturing partner, negotiating favorable terms, and maintaining quality and compliance.
For more guidance and expert insights into navigating the complexities of OEM and ODM when outsourcing manufacturing to China, feel free to contact us. Our team of seasoned professionals is equipped to help you make strategic decisions that align with your business objectives and market dynamics.