Posts Tagged ‘Electronics Production’
How Customized Manufacturing Drives Precision and Efficiency
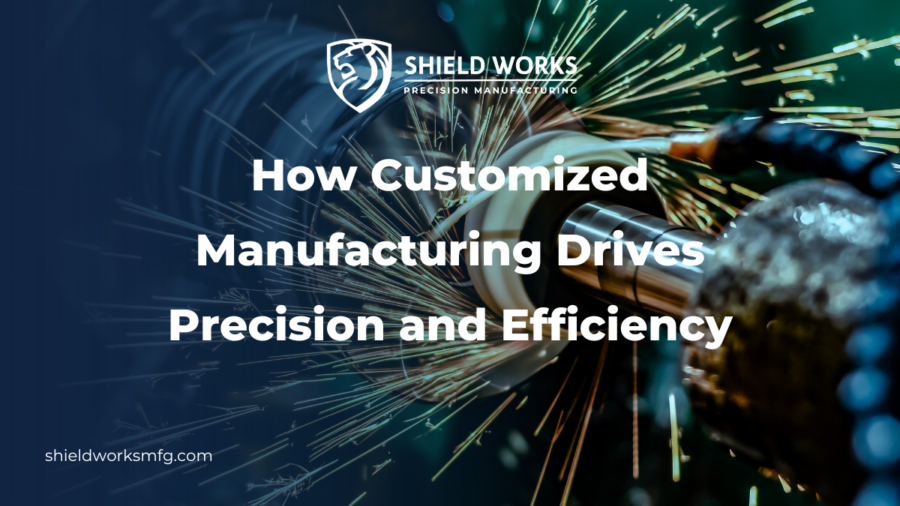
In the world of manufacturing, precision and efficiency are two of the most critical factors in producing high-quality products. Many businesses, both large and small, are turning to customized manufacturing solutions to meet their specific needs and improve their production processes. In this blog, we explore how customized manufacturing in China can help companies achieve unparalleled precision and efficiency, leading to better products and higher profitability.
What is Customized Manufacturing?
Customized manufacturing refers to the process of designing and producing goods based on the specific requirements of a customer. Unlike mass production, which relies on standard designs and large batches, customized manufacturing involves tailoring every step of the production process—from design to materials to production methods—to meet the unique needs of the customer.
Customized manufacturing allows companies to produce products that are not only aligned with their vision but also optimized for functionality, quality, and cost-efficiency. This tailored approach ensures that the final product meets or exceeds industry standards while also fulfilling specific business goals, whether that be market differentiation, performance, or even sustainability.
Why Choose Customized Manufacturing?
Many companies opt for customized manufacturing because it allows them to stand out in competitive markets. By offering products that are specifically designed for a target audience or designed to solve a particular problem, businesses can gain a competitive edge.
Moreover, customized manufacturing can lead to significant cost savings. By using more efficient processes and materials, companies can minimize waste and reduce overall production costs. Additionally, the ability to customize products can allow businesses to control the quality of every component, ensuring consistency and reliability throughout production.
The Benefits of Customized Manufacturing in China
Customized manufacturing in China offers several key advantages that can help businesses optimize their production processes and achieve greater efficiency. Here are some of the main benefits:
Precision
One of the key drivers behind the popularity of customized manufacturing in China is its emphasis on precision. Manufacturers in China are equipped with advanced machinery and software that allow them to create components and products with exceptional accuracy. Whether you’re looking for small, intricate parts or large, complex systems, Chinese manufacturers have the technology and skillset to meet those demands.
Efficiency
Another major benefit of customized manufacturing in China is its emphasis on efficiency. China’s robust supply chain networks and streamlined production processes enable manufacturers to complete orders in a timely manner, reducing lead times and minimizing delays. Moreover, the country’s vast labor force ensures that projects are completed quickly without sacrificing quality.
Cost-Effectiveness
China’s lower labor costs, combined with its large-scale manufacturing capabilities, make it a cost-effective option for customized production. Businesses can take advantage of these cost savings without compromising on quality or precision. Additionally, Chinese manufacturers often offer flexible pricing models, which can be adjusted based on production volumes, materials, and other factors, making customized manufacturing in China an appealing option for businesses of all sizes.
Scalability
As businesses grow, so do their production needs. Customized manufacturing in China offers scalability that allows companies to easily increase production volumes without encountering major obstacles. Whether you need a small batch or large-scale production, Chinese manufacturers can adapt their processes to match your needs, ensuring you get the best results no matter the size of the project.
Potential Challenges of Customized Manufacturing in China
Although customized manufacturing in China offers many benefits, it’s not without its challenges. Language barriers, cultural differences, and time zone issues can create misunderstandings. Additionally, navigating the complexities of Chinese regulations and intellectual property protection can be tricky for businesses unfamiliar with the local market.
To mitigate these risks, it’s crucial to work with an experienced sourcing agent or consultant who understands the nuances of Chinese manufacturing.
How to Find the Right Customized Manufacturing Partner in China?
Finding the right customized manufacturing partner in China can be a transformative decision for your business, offering numerous opportunities for cost savings, quality, and innovation. However, navigating the vast landscape of manufacturers can be daunting, especially when seeking a partner who aligns with your unique needs and business objectives.
To make the right choice, it’s important to focus on several key factors. Start by thoroughly assessing potential partners’ expertise, industry experience, and capacity to meet your specific requirements. This includes looking for a partner with a solid track record in producing the type of products you require and the ability to scale production as your business grows. Additionally, communication and transparency are essential to ensure that expectations are aligned and that there are no surprises down the line. Thorough due diligence, including factory visits, checking certifications, and gathering client testimonials, will also help you identify the most reliable partner for a successful long-term collaboration.
If you’re ready to explore customized manufacturing options in China, our team at Shield Works is here to help. Contact us today to discuss your manufacturing project. We’re committed to delivering precision, efficiency, and quality in every product we produce.
How Automation is Redefining Efficiency in Electronics Production
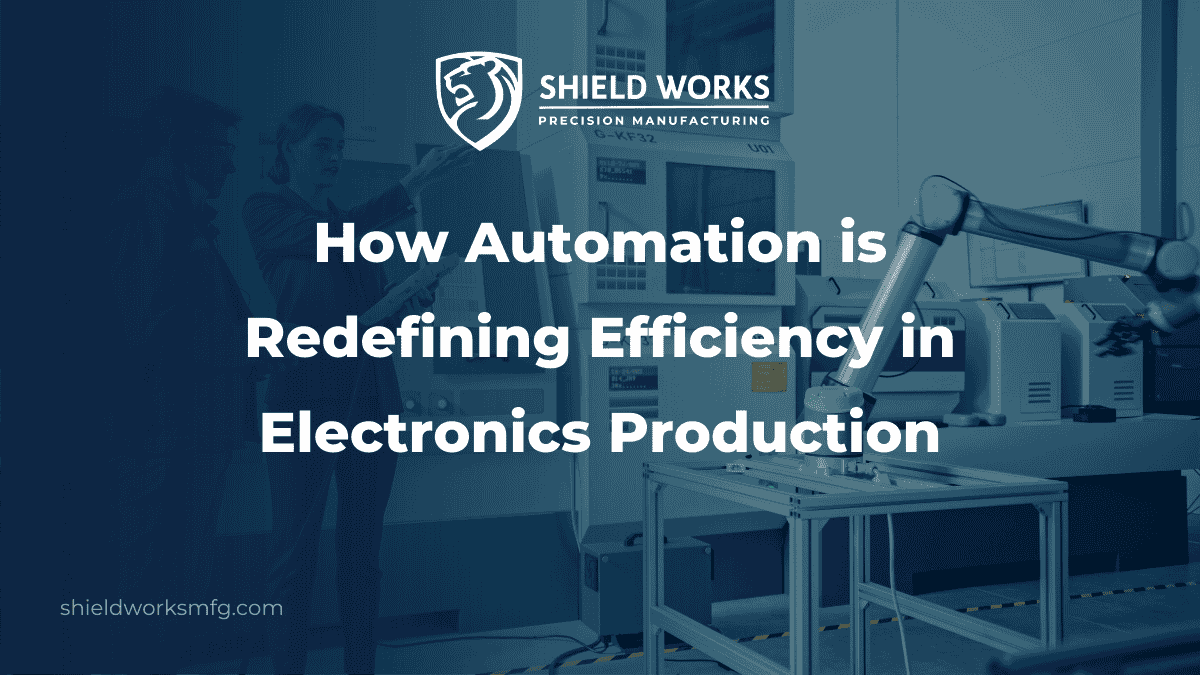
The landscape of electronics production is undergoing a remarkable transformation. As industries face increasing pressure to enhance efficiency, reduce costs, and improve product quality, automation has emerged as a game-changer. This blog delves into how automation is redefining efficiency in electronics production, highlighting its benefits, challenges, and future implications.
The Rise of Automation in Electronics
Automation is not a new concept; however, its application in electronics production has significantly accelerated in recent years. The integration of advanced technologies such as robotics, artificial intelligence (AI), and the Internet of Things (IoT) has made it possible to streamline production processes. With the demand for electronics soaring—spurred by advancements in consumer technology, automotive innovations, and smart devices—manufacturers are compelled to adapt. Automation enables companies to respond to market demands swiftly while maintaining high production standards.
Enhancing Operational Efficiency
One of the most compelling advantages of automation in electronics production is its capacity to enhance operational efficiency. Automated systems can perform repetitive tasks with precision and speed, reducing human error and increasing output. For instance, robotic arms can assemble components faster than manual labor, minimizing assembly time and allowing for greater production volume. This efficiency not only speeds up the production line but also reduces lead times, allowing companies to meet tight deadlines and fulfill customer orders promptly.
Moreover, automation systems can be programmed to monitor production processes in real-time, ensuring that any discrepancies or faults are detected immediately. This proactive approach helps maintain product quality and reduces waste, further enhancing efficiency.
Cost Reduction and Resource Optimization
Cost reduction is a significant driving force behind the adoption of automation in electronics production. While the initial investment in automation technology may be substantial, the long-term savings can be significant. Automated systems require fewer labor resources, thereby decreasing labor costs. Additionally, they optimize the use of materials, reducing waste and improving resource allocation.
Automation also facilitates predictive maintenance, which minimizes downtime. By employing sensors and data analytics, companies can predict equipment failures before they occur, allowing for timely maintenance. This reduces the likelihood of costly production halts and ensures that machinery operates at peak efficiency.
Improving Quality and Consistency
Quality control is paramount in electronics production, where precision is crucial. Automation enhances product quality by ensuring consistent performance across manufacturing processes. Automated systems can execute tasks with a level of accuracy that is often unattainable by human operators. For instance, machines can perform intricate soldering processes or delicate component placements with precision, leading to fewer defects and higher-quality products.
Additionally, automation enables rigorous quality assurance processes. Automated inspection systems can analyze products at various stages of production, identifying defects and ensuring that only products meeting quality standards proceed to the next stage. This focus on quality not only enhances customer satisfaction but also strengthens brand reputation.
Overcoming Challenges in Implementing Automation
Implementing automation in electronics production, while highly beneficial, comes with its set of challenges. One of the primary obstacles is the high initial investment required for purchasing advanced machinery and software. This financial burden can be particularly challenging for smaller manufacturers who may lack the capital to make such substantial upfront expenditures. Additionally, integrating automation into existing production lines often necessitates significant modifications, further increasing costs and complexity.
Another critical challenge is the learning curve associated with new technologies. Employees need to be trained to operate, monitor, and maintain automated systems effectively. This training demands time and resources, and there can be a transitional period where productivity might temporarily dip as workers adapt to the new processes. Resistance to change is also a common issue; employees may fear job displacement or feel overwhelmed by the new technology, which can create a challenging work environment.
To mitigate these challenges, manufacturers can adopt a phased approach to automation, gradually integrating automated systems rather than implementing them all at once. This allows for a smoother transition and provides employees with ample time to adapt to new technologies. Investing in comprehensive training programs and fostering a culture of continuous learning can also help ease the workforce into the new automated environment.
Moreover, manufacturers must address the concerns of their employees head-on, providing clear communication about how automation will impact their roles and offering opportunities for skill development. By involving employees in the transition process and demonstrating the long-term benefits of automation, manufacturers can reduce resistance and create a more collaborative atmosphere. Finally, partnering with technology providers for ongoing support and maintenance can ensure that automated systems continue to operate smoothly, minimizing disruptions and maximizing productivity.
Conclusion
Automation is undeniably reshaping the landscape of electronics production. By enhancing operational efficiency, reducing costs, improving quality, and paving the way for future innovations, automation stands as a key driver of success in the industry. As companies navigate this transformative journey, embracing automation will be critical to remaining competitive in an ever-evolving market.
If you’re interested in exploring how automation can revolutionize your production processes or have any questions, contact us today! Our team is here to help you leverage the power of automation to enhance your operational efficiency and achieve your business goals.